Digital cask filling solution could save Scottish whisky industry millions
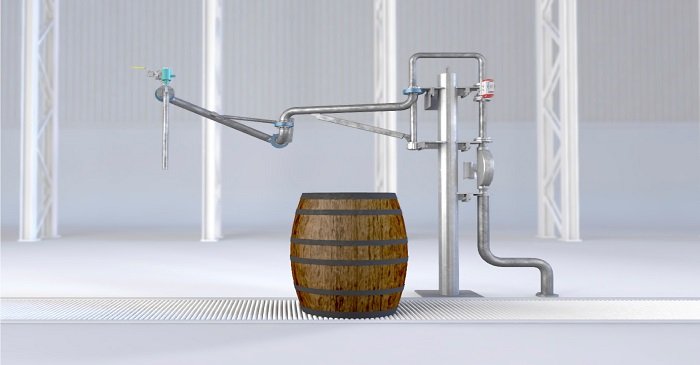
Researchers at the University of Strathclyde’s Advanced Forming Research Centre (AFRC), a specialist technology centre within the National Manufacturing Institute Scotland (NMIS), have collaborated with industrial partners to devise a digital whisky cask filling process that could save Scotland’s £5.5 billion whisky industry millions of pounds each year in inventory costs.
Bringing advances in industry 4.0 to a manufacturing process that is steeped in tradition, project partners include the AFRC, technology giant Siemens, world leading drinks company Diageo, and leading process control system and electrical experts, Kigtek.
The Innovate UK funded project is set to save distillers significant capital expenditure from logistics and warehouse space for additional casks by tackling the problem of inconsistent cask filling levels resulting from overspill, under fill and foaming.
The project partners worked together to create an industry demonstrator, complete with innovative whisky cask filling test rig and cyber-physical system, incorporating a digital twin that replicates the physical process in a virtual environment.
Providing real-time data on fill volume, the digital design allows operators to account for every drop that has gone into each cask, achieving a better than 99% fill consistently, on a 200-litre cask, in under one minute.
Cask production accounts for 10% to 20% of the overall cost of whisky production, and with a minimum of three years required for Scotch whisky maturation, consistent and precise fill levels are extremely important for distillers. Diageo, for instance, holds over 11 million casks in maturation at one time so to achieve close to maximum fill would save significant costs.
Traditional Scotch whisky casks are handmade using oak, meaning variation in the volume that each can accommodate, making the project particularly challenging.
The digital approach is set to revolutionise industry equipment, allowing it to offer a high degree of repeatability, with additional improvements to health and safety of operators, and enhanced environmental impact due to reduced waste.
Danny McMahon, Digital Manufacturing Team Lead at the AFRC, said:
The digital twin system achieved as the output of this project will allow Scotland’s whisky industry to truly embrace industry 4.0 using data to digitise a traditional process.
"The collaborative nature of the project combined the centre’s design and digital manufacturing expertise with industry partners Siemens instrumentation know-how, Kigtek’s process and control understanding and Diageo’s industry knowledge, to devise a revolutionary system with immense benefits for a multi-billion pound industry that is crucial to Scotland’s economy.
“Industrial Internet of Things (IIoT) development sector wide, is changing the way we manufacture, with new designs, processes and innovation allowing for a modern approach that comes with huge savings in costs, time and energy consumption.
Latest news from across the NMIS Group
-
Maritime project delivers 10% emissions cut and 90% faster lead times using large scale additive manufacturing
Thursday, August 28, 2025 -
Apprentices plug into digital tools in manufacturing skills drive
Monday, July 14, 2025 -
Funding injection set to expand NMIS’s semiconductor manufacturing capabilities to create UK centre for advanced packaging
Wednesday, July 2, 2025 -
Advanced remanufacturing could transform wind turbine repairs and cut emissions
Wednesday, June 4, 2025 -
Harris Tweed® weaves next-generation technology into centuries-old craft
Thursday, May 29, 2025 -
Major inward investment secured with US manufacturer
Wednesday, May 21, 2025 -
Superplastic forming community to gather in Scotland for Euro SPF 2025
Monday, April 14, 2025 -
£9 million funding boost to bring key semiconductor manufacturing capability to Scotland
Thursday, March 20, 2025 -
NMIS joins space race with unveiling of second-stage vehicle demonstrator
-
New Digital Process Manufacturing Centre unlocks emerging technology for Scottish industry
Thursday, February 27, 2025 -
Plugging AI skills gaps critical for future of shipbuilding industry
Thursday, February 20, 2025 -
Construction begins on NMIS supported £9 million ETZ EnergyWorks in Aberdeen
Friday, November 22, 2024 -
New £5.5M manufacturing centre set to boost UK’s net-zero goals and drive economic growth
Wednesday, November 6, 2024 -
Startup aims to peel back plastic use with onion skin packaging
Wednesday, October 9, 2024 -
AFRC and ATI forge partnership to boost aerospace materials innovation
Wednesday, October 9, 2024 -
NMIS strengthens leadership team with two new appointments
Tuesday, September 17, 2024 -
3D printing helps young entrepreneur’s therapy device blossom
Thursday, September 5, 2024 -
AFRC achieves world-class accreditation for mechanical testing
Monday, August 5, 2024 -
Factory simulation helps Scottish confectioner hit the sweet spot
Monday, July 22, 2024 -
NMIS hires industry heavyweight as electrification lead
Monday, July 1, 2024 -
NMIS bolsters board with two industry powerhouses
Monday, June 17, 2024 -
£14 million funding to support Glasgow manufacturers to become greener and more productive
Wednesday, May 8, 2024 -
Hybrid approach to titanium manufacturing boosts UK aerospace opportunity
Thursday, April 18, 2024 -
Pioneering forging research hub puts Scotland at the forefront of advanced engineering
Thursday, March 21, 2024 -
Apprenticeship matchmaking tool aims to close Scotland’s manufacturing skills gap
Thursday, March 7, 2024 -
Scottish SMEs receive £1M support to explore additive manufacturing
Wednesday, February 7, 2024 -
Decking company elevated to new heights with ‘floating’ gardens
Tuesday, December 19, 2023 -
AFRC and ITP Aero win EPSRC Prosperity Partnership Award
Wednesday, November 29, 2023 -
Groundbreaking project to bring high-value 3D printing to UK manufacturing
Wednesday, August 9, 2023 -
Cutting-edge demos boost small business growth in the UK’s machining sector
Thursday, July 27, 2023 -
National Manufacturing Institute Scotland to help deliver Scotland’s first energy incubator and scale-up hub
Wednesday, July 12, 2023 -
Ground-breaking NMIS facility paving the way for the future of manufacturing in Scotland
Wednesday, June 21, 2023 -
Net-zero future for UK wind industry accelerating with growth of new industry body
Tuesday, June 13, 2023 -
Striking a hammer blow for metals recycling
Wednesday, May 3, 2023 -
Scotland’s manufacturing R&D anchor bolsters leadership team with new talent
Monday, March 6, 2023 -
The future’s looking green for Scotland’s manufacturers as the Lightweight Manufacturing Centre commissions new equipment
Thursday, February 16, 2023 -
Major milestone achieved at Scotland’s new flagship manufacturing R&D facility
Friday, February 10, 2023 -
Become a sustainability champion for free with the Manufacturing Skills Academy
Monday, December 19, 2022 -
New supply chain R&D project aims to revolutionise zero-emissions shipbuilding and create Scottish jobs
Thursday, December 1, 2022 -
Works begin at Ayrshire’s new manufacturing innovation centre
Thursday, November 24, 2022 -
Scotland’s innovation magnet attracts global tech firms as it opens its membership programme
Thursday, October 13, 2022 -
Five minutes with…Jennifer MacDonald
Tuesday, October 11, 2022 -
Five minutes with… Daniele Marini
Tuesday, October 11, 2022 -
Five minutes with… Anastasia Khatunsteva
Thursday, October 6, 2022 -
Research ties between Scotland and Australia could advance shipbuilding on the Clyde
Friday, September 23, 2022 -
National Manufacturing Institute Scotland appoints former UKRI Challenge Director as Chief Executive Officer
Monday, September 5, 2022 -
New course with key industry players to boost photonics skills
Thursday, August 18, 2022 -
Forging ahead
Wednesday, August 17, 2022 -
Orkney manufacturers given first access to national net-zero initiative
Tuesday, July 5, 2022 -
NMIS celebrating Scottish manufacturing with the FM’s award for manufacturing leadership
Thursday, June 16, 2022 -
Strathclyde, SSE Renewables & Renewable Parts sign joint MoU to develop a sustainable wind sector
Wednesday, June 15, 2022 -
A digital future for the process industries with new Ayrshire technology centre
Thursday, June 9, 2022 -
Key equipment arrives at Boeing R&D facility in Scotland
Wednesday, June 1, 2022 -
Pioneering cross border collaboration provides crucial support to UK forging and forming community
Wednesday, June 1, 2022 -
Wind turbine blade recycling project powers up at the Lightweight Manufacturing Centre
Friday, May 20, 2022 -
NMIS prepares for MACH debut
Thursday, March 31, 2022 -
Two new AFRC Tier Two Members accelerating traditional manufacturing methods into the 21st century
Tuesday, March 8, 2022 -
NMIS HQ update: construction reaches final stages
Friday, March 4, 2022 -
Rotary forge heading to 'steel city' from Renfrewshire
Monday, February 28, 2022 -
New project set to help manufacturers cut costs and land net-zero targets
Wednesday, February 9, 2022 -
Entries now open for showpiece celebration of Scottish innovation
Tuesday, February 8, 2022 -
University of Strathclyde students aim for a podium finish in NMIS motorcycle racing project
Tuesday, March 8, 2022 -
Fifty fully paid work placements made available for STEM graduates in Scotland
Monday, January 31, 2022 -
The future of manufacturing comes to the AFRC with three new Members and one renewal
Wednesday, January 19, 2022 -
The skill requirements for a net zero future: The Manufacturer in conversation
Thursday, January 13, 2022 -
Manufacturing Skills Academy launches pandemic recovery package to help upskill Scots and boost innovation
Wednesday, December 22, 2021 -
Forging a new future for green energy
Tuesday, December 7, 2021 -
From 3D printer to international catwalk
Wednesday, December 8, 2021 -
NMIS operator, Strathclyde, wins Queen’s Anniversary Prize for Higher and Further Education in Advanced Manufacturing
Friday, November 26, 2021 -
£2million pilot led by Scottish researchers to develop UK’s first wind turbine blade recycling project gets go-ahead
Thursday, November 18, 2021 -
£1.2m project extends life of parts in quest to help manufacturers tap into net zero economy
Thursday, November 18, 2021 -
Manufacturing a Net-Zero Future: in-person conference open for registration
Wednesday, October 20, 2021 -
NMIS and Boeing officially open new R&D facility in Renfrewshire
Tuesday, October 5, 2021 -
Manufacturing a net-zero future: a conversation with NMIS Chief Operating Officer Sarah Jardine
Tuesday, September 28, 2021 -
Patients recovering from strokes, dystonia and sports injuries could reduce rehabilitation time by 30% with virtual reality gaming platform
Thursday, September 23, 2021 -
National Manufacturing Institute Scotland HQ reaches major construction milestone
-
Free online events with NMIS and Product Design Scotland: navigating the product design process
Wednesday, September 1, 2021 -
NMIS HQ construction update: digital factory is taking shape
Friday, March 26, 2021 -
New partnership set to future proof process manufacturing in Scotland
Monday, August 30, 2021 -
Smart Factory Innovation Hub testbed at NMIS helping Scottish businesses to harness digital technologies
Thursday, May 6, 2021 -
Recycling aeroplanes and turning them into drinks cans: the role of composites in the journey towards net-zero
Thursday, August 26, 2021 -
World renowned Scottish forging and forming research centre opening an office in ‘steel city’
Thursday, August 12, 2021 -
Tooling specialist chisels out agreement for another three years
Tuesday, August 10, 2021 -
AFRC and MAPAL drive tooling manufacture into the future
Wednesday, May 12, 2021 -
Augmented reality project to help train surgeons around the world on ‘hyper-real’ models of organs
Wednesday, July 21, 2021 -
Every day’s a school day: skills development and its vital role in manufacturing, industry 4.0, and the growth of the Scottish economy
Tuesday, June 15, 2021 -
New capability network will help businesses across Scotland access support and unlock innovation
Thursday, June 10, 2021 -
NMIS HQ construction update: from steel to timber and a heather coloured roof
Monday, May 31, 2021 -
Boeing getting ready for lift off from Westway, Renfrew with NMIS
Wednesday, May 19, 2021 -
New local collaboration gives young people in care a pathway into manufacturing roles
Wednesday, May 12, 2021 -
NMIS launches new scheme to support STEM graduates into employment amid pandemic
Friday, March 19, 2021 -
Three diverse new Tier Two Members join the AFRC
Thursday, March 18, 2021 -
Circular economy project set to ensure clean energy solutions don’t increase landfill waste
-
AFRC welcomes Booth Welsh with iTech
-
AFRC welcomes global technology giant Hewlett Packard Enterprise as Tier Two Member
Wednesday, January 20, 2021 -
Construction underway on flagship National Manufacturing Institute Scotland facility
Tuesday, December 15, 2020 -
NMIS to help transport operators navigate Covid-19 safety measures
Wednesday, December 9, 2020 -
Making Scotland’s future - recovery plan for the manufacturing sector
Friday, December 4, 2020 -
Global companies strengthen their commitment to AFRC to deliver better customer solutions
Tuesday, November 24, 2020 -
Strathclyde and partners to deliver satellite constellation project
Thursday, November 19, 2020 -
Sustainability top of the agenda for NMIS as it joins new additive manufacturing body
Tuesday, October 27, 2020 -
NMIS offers free training resources and a new online CPD course to help individuals upskill from home
Thursday, October 22, 2020 -
High-tech software company Bellrock Technology Ltd joins AFRC as latest Tier Two Member
Monday, October 12, 2020 -
AFRC announces new partnership with Theorem Solutions
Thursday, October 8, 2020 -
Scottish project ‘reinvents the wheel’ with flat-pack hydro-energy solutions for Africa
Monday, October 5, 2020 -
New tool will help Covid response technologies gain necessary approvals
Wednesday, September 23, 2020 -
AFRC welcomes Kigtek as latest Tier 2 member
Friday, September 18, 2020 -
NMIS Boeing programme takes off from Westway, Renfrew
Monday, September 14, 2020 -
AFRC Welcomes ROCOL as new Tier Two Member
Thursday, October 8, 2020 -
University of Strathclyde at the forefront of projects helping small and medium sized manufacturing firms in Scotland
Wednesday, July 29, 2020 -
NMIS donates 10,000 face visors to help charities move forward from lockdown
Wednesday, July 22, 2020 -
Digital cask filling solution could save Scottish whisky industry millions
Tuesday, July 14, 2020 -
Transvalor joins the AFRC as the first Tier One Partner in support of new FutureForge facility
Tuesday, July 7, 2020 -
Made in Scotland: the new wind turbine blade set to make green energy even greener
Wednesday, July 1, 2020 -
Contract awarded for construction of flagship National Manufacturing Institute Scotland facility
Friday, May 29, 2020 -
National Manufacturing Institute Scotland leadership team bolstered with CEO appointment
Tuesday, May 26, 2020 -
Planning permission granted for construction of National Manufacturing Institute Scotland facility
Monday, April 6, 2020 -
Boeing touches down in Scotland with new strategic alliance
Monday, April 6, 2020 -
NMIS Insights: National Manufacturing Institute Scotland launches its first event series
-
Planning permission submitted for National Manufacturing Institute Scotland
-
Why the oil and gas sector needs to embrace Additive Manufacturing
-
AFRC Tier Two Membership is measuring up for leading precision engineering firm