Our capabilities
We're providing manufacturers with the means to explore new opportunities, increase and maintain competitiveness while also helping to develop a wide, supportive supply chain.
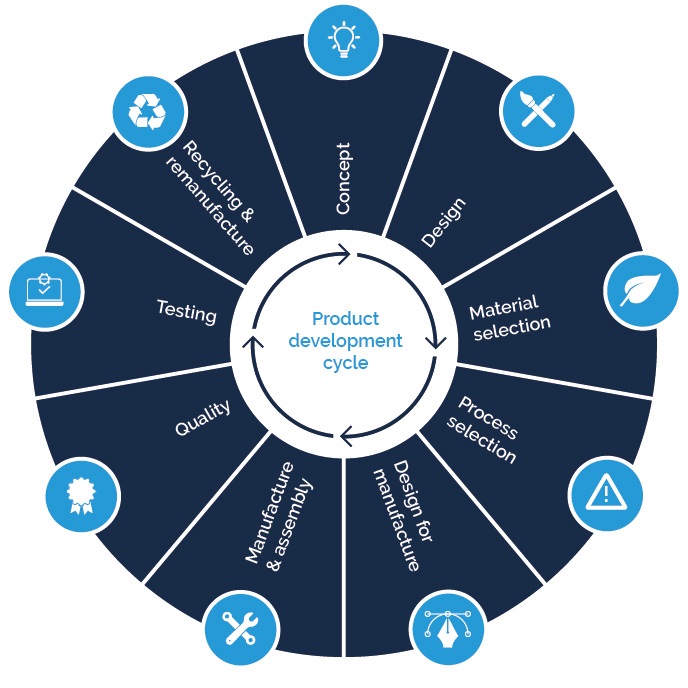
The product development cycle
The types of support we can offer to help your business include:
- Concept
- Design
- Material selection
- Process selection
- Design for manufacture
- Manufacture & assembly
- Quality
- Testing
- Recycling & remanufacture