FutureFibre
Overview
Carbon fibre production requires significant amounts of fossil fuels and energy, with temperatures of up to 1000°C needed to create the fibre material. It's also costly and is up to 10 times as expensive as steel.
With a climate crisis solution high on the agenda for many manufacturers, the search for an eco-friendlier alternative to traditional carbon fibre is on.
The project
We're combining the experience of academics and industry professionals, and the infrastructure and resources needed to delve deeper into alternatives to the traditional fibre manufacturing process.
Our approach will see us improve the green credentials of the production process and employ new methods of recycling existing carbon fibre and thermoplastic fibre materials.
The aim is to deliver an effective, lightweight solution with a significantly reduced carbon footprint.
Contact us
The FutureFibre team is keen to hear from biomass suppliers across Scotland. Get in touch here.
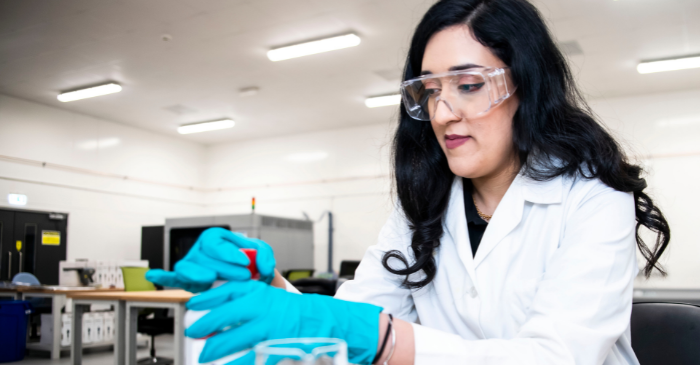
Sairah Bashir, Research and Development Engineer, LMC
Through working with the Lightweight Manufacturing Centre companies can access world-class expertise and technologies. Contact us today.
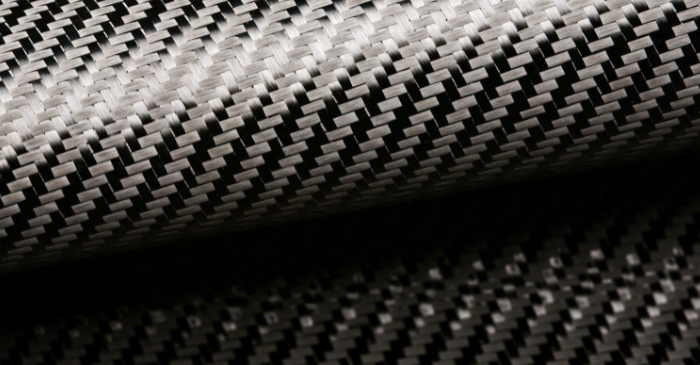
Xplore fibre spinning rig
We've recentlly taken delivery of some very special equipment. A benchtop laboratory scale system that can produce melt-spun fibres from a small quantity of material, the fibre spinning rig is ideal for early fibre formulation screening and development. The equipment is modular in design, so it can also be equipped with other modules to produce materials, such as tapes, films and granules.