Stratellite is an NMIS-led initiative unlocking opportunities in Scotland’s growing space sector.
Led by the Lightweight Manufacturing Centre (LMC), the project is developing an easy-to-reconfigure exploratory production line, designed to automate the precision manufacturing processes required for large satellite structures.
At the heart of the project is an innovative, modular, and scalable production system, designed to adapt to evolving space manufacturing needs.
A key part of the project is the development of a demonstrator, showcasing advanced automation, digital manufacturing, and composite processing techniques. This highlights how flexible, high-precision production can drive efficiency, reduce costs, and accelerate satellite manufacturing.
The technology is being developed with smaller businesses in mind, ensuring it is accessible, cost-effective, and easy to adopt.
The approach enables companies across multiple sectors to become more agile, explore new products and markets, and scale production without requiring large upfront investment.
Showcasing innovation: Stratellite at Space-Comm Expo
To demonstrate the potential of Stratellite, the NMIS team has also developed a recoverable second-stage launch vehicle concept, unveiled at Space-Comm Expo 2025. This proof-of-concept highlights how advanced materials, digital manufacturing, and additive manufacturing can revolutionise space vehicle design.
On display was a concentric liquid oxygen (LOX) and fuel tank, a key component of the concept, demonstrating NMIS’s expertise in lightweight structures, automation, and high-precision manufacturing. The project also showcases scalable solutions to help space manufacturers reduce risk and optimise performance.
This work aligns with Scotland’s ambition to lead in space manufacturing, supporting a sustainable and scalable space economy. By working with companies of all sizes, NMIS is helping drive cost-efficient, high-performance solutions for the next generation of satellite and launch vehicle production.
Meet the team
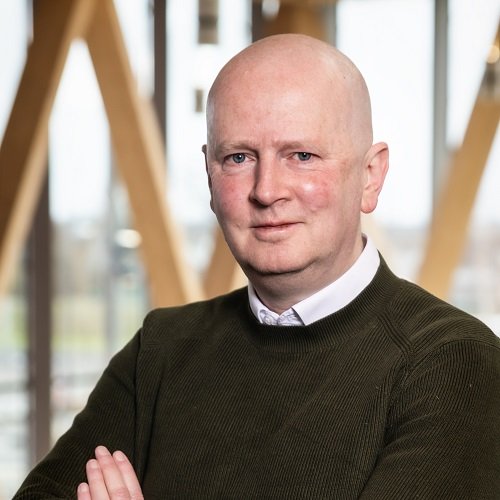
Iain Bomphray
Director, Lightweight Manufacturing Centre
Iain joined in August 2019 as Director of the Lightweight Manufacturing Centre (LMC), supporting industry with funding, skilled staff, facilities, and research.
A Chartered Engineer and Fellow of the Institute of Mechanical Engineers, he has led lightweight structural solutions across sectors, including Automotive, Aerospace, Marine, Rail, and Formula One, where he was Chief Engineer at Red Bull Technologies. He later served as Chief Technical Specialist at Williams Advanced Engineering, focusing on high-volume composite applications.
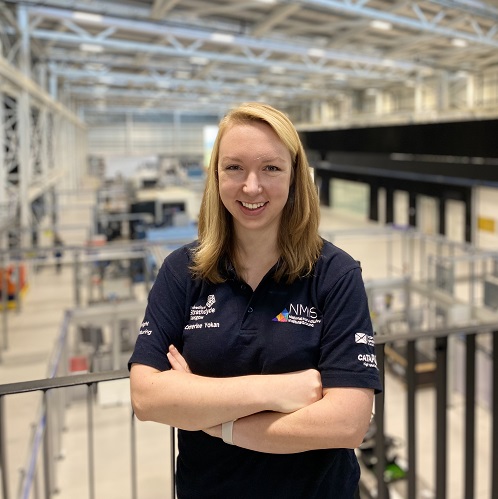
Catherine Yokan
Senior Research & Development Engineer
Catherine joined the Lightweight Manufacturing Centre (LMC) as a Senior R&D Engineer, leading industrial research projects in lightweighting, with a focus on polymers and fibre-reinforced composites.
With degrees in physics and production engineering, she specialises in composite design, materials testing, process optimisation, and end-of-life analysis. Catherine has gained extensive experience at 3M Company, NASA, and the Fraunhofer Institute IFAM. She currently leads the development of a demonstrator second-stage launch vehicle, supporting the growth of space manufacturing in Scotland.
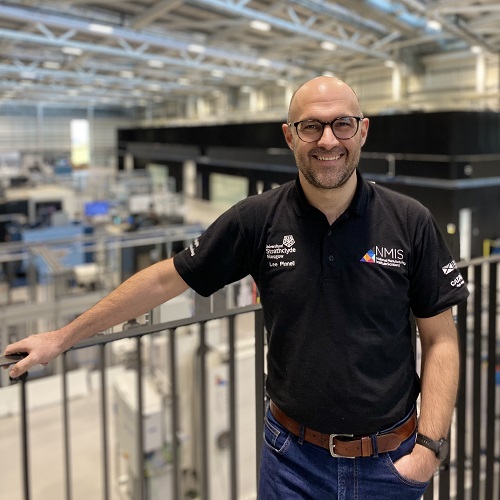
Lee Pinnell
Operations Manager
Lee joined the Lightweight Manufacturing Centre (LMC) to lead day-to-day operations, ensuring the highest standards in Health & Safety, Quality, and NMIS operational excellence.
With extensive experience in lightweight material manufacturing, he has worked across Aerospace, F1, Healthcare, Defence, Automotive, and Vehicle Prototype Build. Lee also serves as the project lead for the Stratellite and Photonics project, demonstrating his expertise in leadership and advanced technology initiatives.
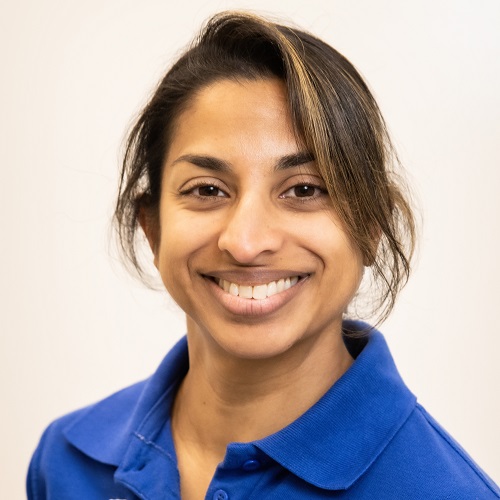
Kareema Hilton
Machining Applications Theme Lead
Kareema joined National Manufacturing Institute Scotland to deepen her expertise in aerospace component manufacturing, focusing on design for manufacture and machining excellence.
With a background in aeronautical engineering, she has worked at ClydeSpace and the Advanced Manufacturing Research Centre, gaining hands-on experience in aerospace manufacturing. Initially intending to return to a design-focused role, she discovered a passion for machining metallic parts, which has driven her career ever since. Kareema continues to apply her expertise in machining within the aerospace sector, contributing to innovation and advanced manufacturing practices.
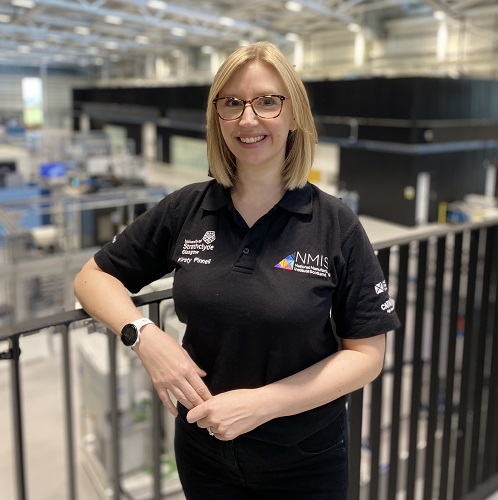
Kirsty Pinnell
Composites Engineer
Kirsty joined the Lightweight Manufacturing Centre (LMC) as a Composites Engineer, bringing over 15 years of experience in lightweight composite structures.
She holds an MEng in Mechanical Design Engineering from the University of Glasgow and an MSc in Motorsport Engineering with Management from Cranfield University. Previously a Senior Composite Design Engineer at Williams Racing in Formula 1, Kirsty now specialises in NX CAD design and analysis. She also leads collaborative initiatives, including Product Lifecycle Management (PLM) implementation and mentoring engineering students.
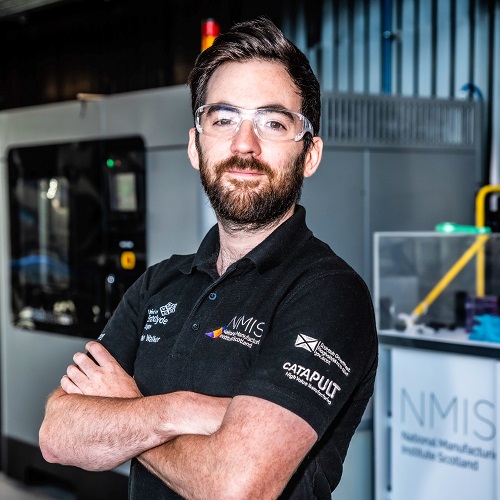
Dickon Walker
Polymer AM Theme Lead
Dickon, a Research & Development Engineer within the Polymer Additive Manufacturing (AM) team at NMIS since January 2022, has been instrumental in supporting companies with the adoption and development of their own AM capability. His primary focus involves identifying suitable applications and adding value wherever possible. He brings a wealth of experience to his role, having previously founded and grown several start-up businesses in the AM, Product Development, and Space sectors. Dickon is a graduate of Product Design Engineering from the University of Strathclyde in 2013.
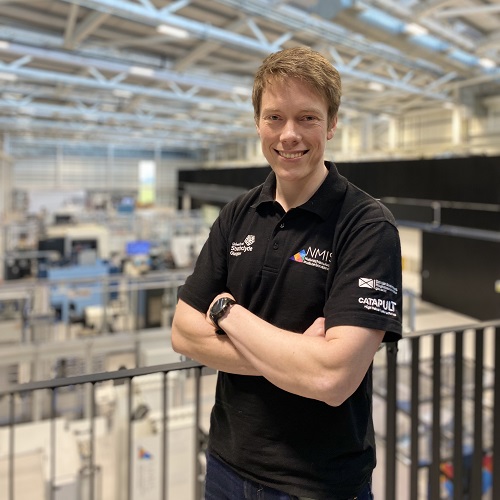
Niklas Meyn
Composites Technician
With nearly a decade in aerospace engineering, Niklas specialises in composite structure design. With over six years in Wind Energy, his expertise covers structural design, manufacturing, full-scale testing, and certification. Most recently, he led blade design for a 100m rotor, overseeing load studies, control software, aerodynamic design, and manufacturability. Previously, he worked on a wind-assisted propulsion system for cargo ships, conducting 2D CFD studies and developing fuel reduction analysis tools. Before Wind Energy, he contributed to the automotive sector, focusing on lightweight jigs and fixtures, from design to installation and maintenance.
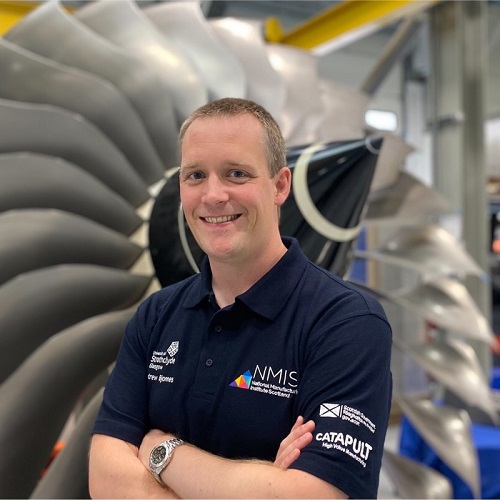
Andrew Bjonnes
Research & Development Engineer
Andrew brings a wealth of experience, previously at QMass Ltd as a production planner and manufacturing engineer. His expertise includes electrode design for EDM and fixture creation for conventional machining, showcasing his comprehensive understanding of the manufacturing process. Proficient in CAD design, particularly SolidWorks, he excels in offline programming with HyperMill and HyperCad-S. Andrew prioritizes quality, adhering to ISO 9001:2015 and Lean Manufacturing/5S principles. Skilled in project management, he ensures stakeholder collaboration for project delivery. Andrew actively contributes to method development, evaluating manufacturing methods and providing improvement reports. He also plays a crucial role in staff training, emphasizing personal and organizational growth.
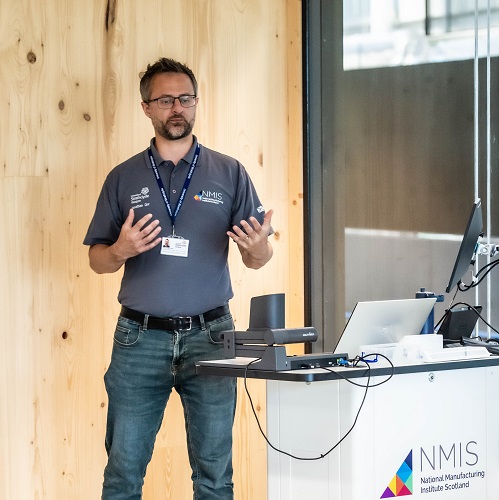
Jon Orr
Space Manufacturing Lead
Jon, a seasoned leader in the space sector, holds a Physics degree and brings over a decade of industry experience, specializing in blue-sky research and development. With more than 8 years at NMIS, he has played a key role in business development and strategy, ensuring NMIS's ability to cater to businesses of all sizes. Jon's dedication extends to the space initiatives at NMIS, where he has been actively involved for 3 years. He currently leads the HVMC Space Community of Practice and is a notable member of influential groups such as the Space Scotland Environment Task Force, the Scottish All-Party Parliamentary Group for Space, and the Space Energy Initiative. Jon's comprehensive engagement underscores his commitment to driving innovation and collaboration in the space industry at both local and national levels.
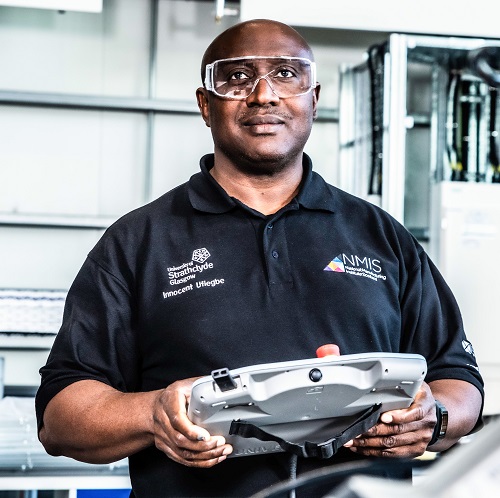
Innocent Ufiegbe
Composites Technician
Innocent is a seasoned Manufacturing professional with over a decade of industry experience. He holds an HND in Mechanical Engineering (Production option) and has worked in various roles, including Production Coordinator and Process Officer. Passionate about continuous learning, Innocent successfully completed a Master of Research (MRes) in Environmental Analysis & Assessment, obtaining his certificate from Heriot-Watt University. He also has experience as a Work Preparator with Shell Petroleum. With a diverse background, he now serves as a Manufacturing Composites Technician at NMIS, contributing his expertise to innovative projects.
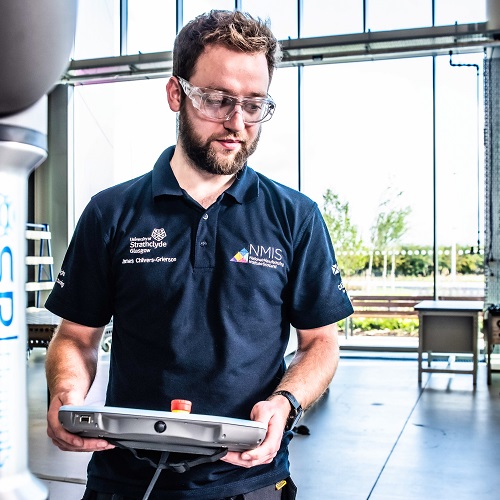
James Chilvers-Grierson
Composites Technician
James brings a wealth of expertise to the LMC team. With a background in Naval Architecture and Marine Engineering from Strathclyde University, he joined LMC in June 2019. With over 4.5 years of hands-on experience in various composite manufacturing techniques, including hand layup, RTM, and prepreg layup, James is well-versed in both in and out of autoclave curing methods. In his role as LMC technical lead, he plays a pivotal role in managing workshop assets and ensuring compliance with health and safety standards.

Ruoyu Huang
Process Modeller
Ruoyu, a Process Modeller at the Lightweight Manufacturing Centre (LMC) at NMIS, specializes in mathematical and numerical modeling of composite structures and manufacturing processes. His expertise encompasses process modeling for resin infusion of full-scale wing covers in collaboration with leading aerospace companies. He also possesses strong skills in structural analysis and damage modeling of multi-material structures with complex modules and connectors under various loadings. Ruoyu initiated the modeling and programming of robotic systems at LMC, aiming to create Digital Twins for automated composite manufacturing and other industry processes. His key responsibilities include modeling manufacturing processes, structural analysis, constitutive modeling of materials, robotic simulation and programming, developing advanced modeling tools, leading and delivering projects, and engaging with key NMIS partners.
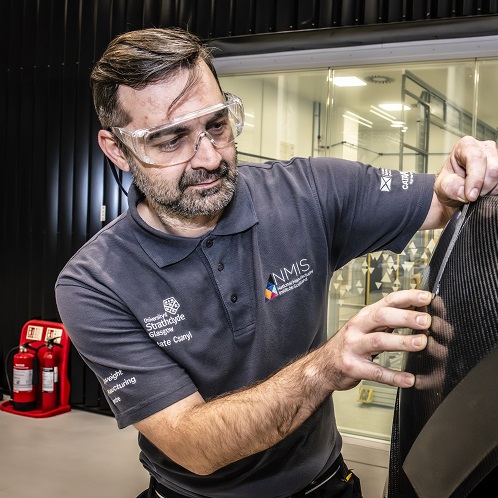
Mate Csanyi
Composites Technician
Mate is an experienced manufacturing professional with a rich and diverse background spanning over a decade. Prior to his role at NMIS, he served as an Assembly Supervisor at METYX Hungary Ltd., bringing five years of experience in overseeing assembly operations. Mate also held various positions at Premier Composite Technologies in Dubai, UAE, including Production Coordinator, Senior Supervisor, and Supervisor, accumulating over six years of full-time experience in composite manufacturing. His journey in the manufacturing industry began as a Laminator at Areva Wind Gmbh in Bremenhaven, Germany, where he gained valuable insights into wind turbine component fabrication. Mate's expertise extends to boat building, having worked both as a Boat Builder at Premier Composite Technologies in Dubai and as a self-employed Boat Builder in Hungary. With his extensive experience and versatile skill set, Mate continues to make significant contributions to the manufacturing sector.
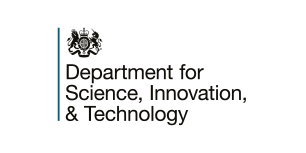
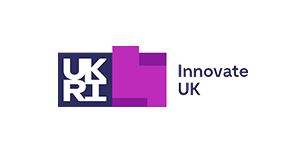
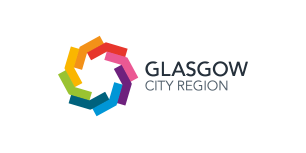
This project is part-funded by the Glasgow City Region Innovation Accelerator programme.
Led by Innovate UK on behalf of UK Research and Innovation, the pilot Innovation Accelerator programme is investing £100m in 26 transformative R&D projects to accelerate the growth of three high-potential innovation clusters – Glasgow City Region, Greater Manchester and West Midlands.
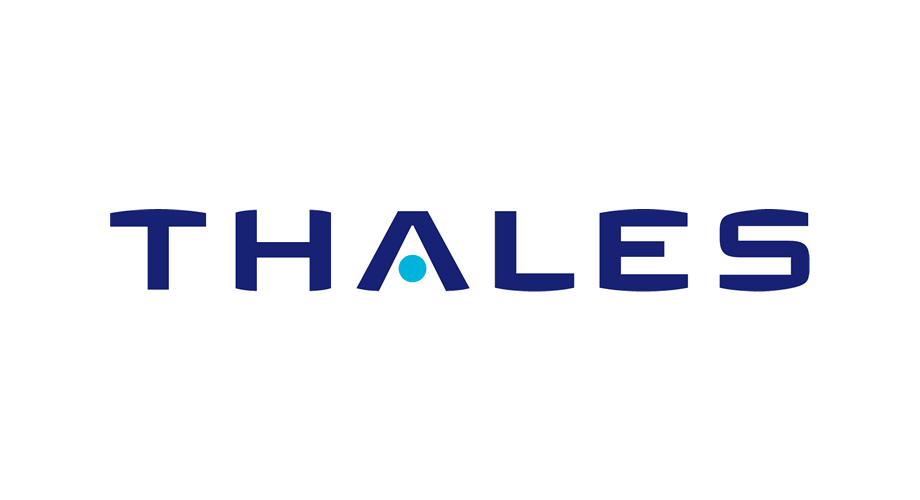