ReMake
Creating a pipeline of highly skilled green jobs and reduce waste and carbon emissions.
Contact our teamThe ReMake Glasgow project is developing a first-of-its-kind national ReMake hub within the NMIS Digital Factory. The hub will provide the skills and technologies needed to support ambitious manufacturers of all sizes to adopt circularity and extend the life of products and parts.
The aim is to achieve a 99% reduction in CO2 compared to manufacturing from new through processes such as remanufacturing, refurbishing and repairs.
With under 2% of products manufactured in the UK currently designed and reused in this way, the ReMake hub is set to advance sustainable manufacturing by supporting companies to move towards a circular economy.
This investigates the potential of value retention processes for a twin-screw compressor as an end-use case for ReMake technology development within a test bed context. The results from this test bed are anticipated to have relevance for the general manufacturing industry, academia, and beyond.
The work package lead is Calum Hicks, from NMIS who is working in collaboration with Howden as the industry partner.
This investigates the potential of value retention processes for an aircraft wing panel as an end-use case for ReMake technology development within a test bed context. The results from this test bed are anticipated to have relevance for the aviation industry, academia, and beyond.
The work package lead is Ryan Devine, from NMIS who is working in collaboration with Boeing and British Airways Maintenance as the industry partners.
This investigates the potential of value retention processes for a subsea anchor block as an end-use case for ReMake technology development within a test bed context. The results from this test bed are anticipated to have relevance for the offshore hydrocarbon industry, academia, and beyond. The work package lead is Misael Pimentel.
This investigates the potential of value retention processes for a wind turbine yaw gear as an end-use case for ReMake technology development within a test bed context. The results from this test bed are anticipated to have relevance for the wind energy industry, academia, and beyond.
The work package lead is Ashfaq Mohammad, from NMIS who is working in collaboration with SSE Renewable and Renewable Parts Ltd as the industry partners.
This investigates the potential of value retention innovation support packages that would aid organisations adopt ReMake technologies and practices, such as Circular Business Models, LCA, Design and Cost modelling for ReX and exploitable CPD activities. The results are anticipated to have relevance for the general manufacturing industry, aviation industry, hydrocarbon industry, wind energy industry, academia, and beyond.
The work package lead is Daniel McDaid, from NMIS who is working in collaboration with Scottish Institute for Remanufacture and Strathclyde Business School as the project partners.
This investigates the potential of value retention information being supported through accessible data embedded within a developed digital product passport framework and demonstrator, it is conducting the data integration within a digital ReMake framework that would aid organisations adopt ReMake technologies and practices. The results are anticipated to have relevance for the general manufacturing industry, aviation industry, hydrocarbon industry, wind energy industry, academia, and beyond.
The work package lead is John Reilly, from NMIS who is working in collaboration with ATS Global as the industry partner.
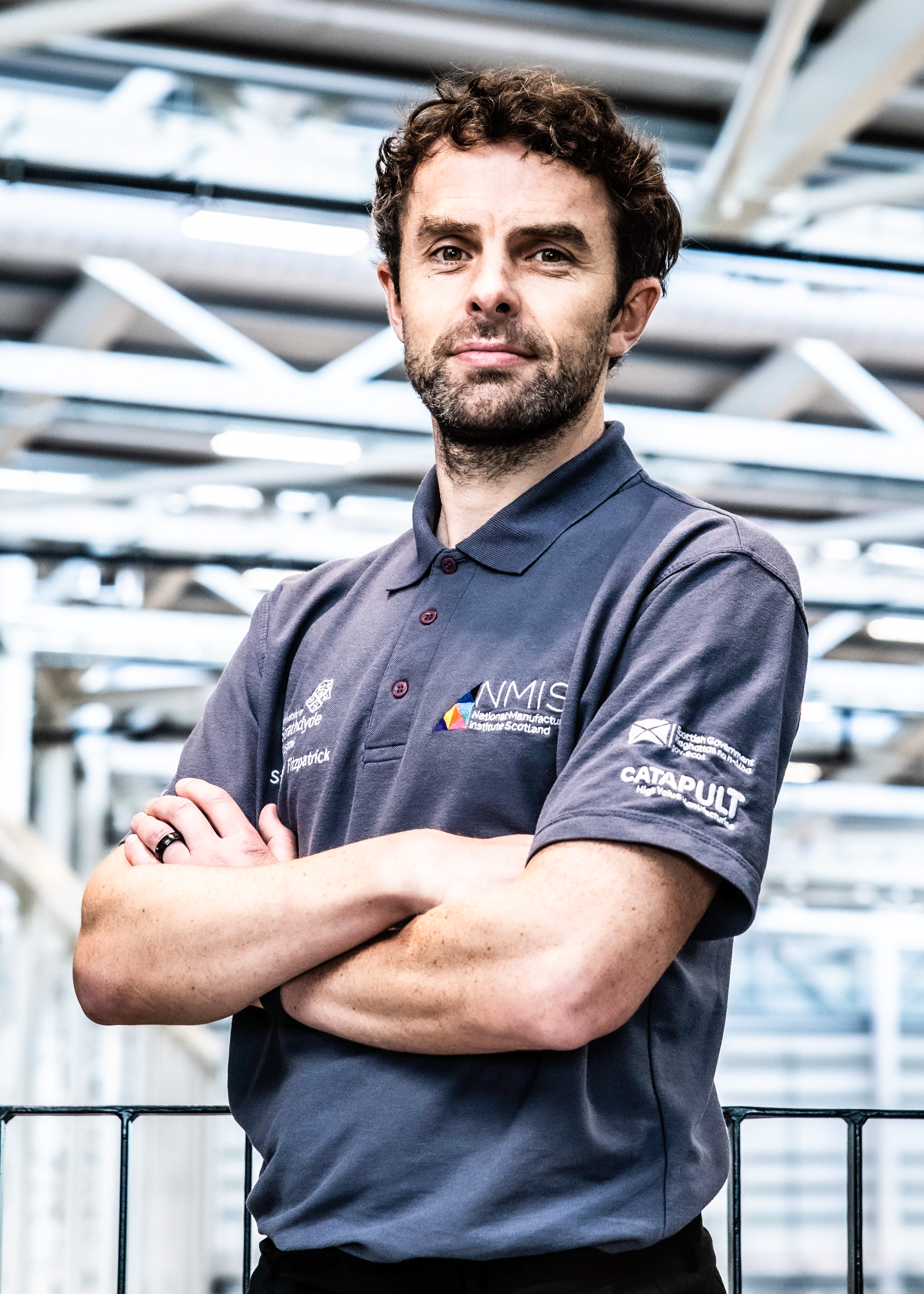
Stephen Fitzpartrick
Digital Factory Director
Stephen is a Fellow of the Institution of Mechanical Engineers. He previously led the NMIS machining and additive research division in his role as Senior Knowledge Exchange Fellow.
Stephen leads the NMIS Digital Factory, one of the five specialist centres within the NMIS Group. He will provide the vision and leadership to drive forward the centre in its ambition to transform the manufacturing landscape in Scotland and the wider UK through spearheading the development of innovative digital technologies applied into manufacturing processes.
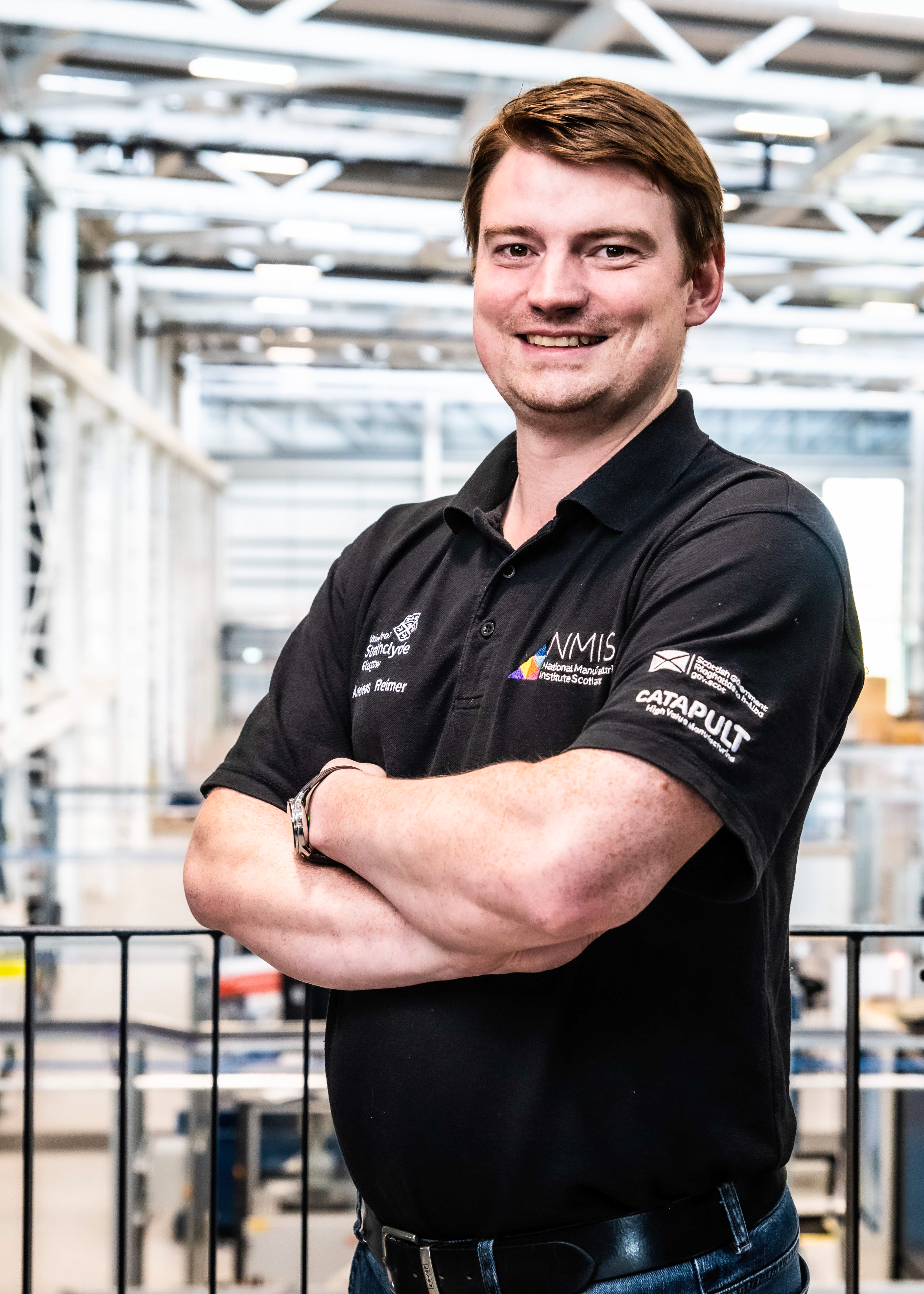
Andreas Reimer
ReMake Lead, Digital Factory
Andreas is a Strategic Program (Theme) Lead and Manufacturing (R&D) Engineer with expertise in machining optimisation, additive manufacturing, and remanufacturing at NMIS. He completed his Engineering Doctorate at the University of Strathclyde, with a specific focus on the optimization of high-speed die machining processes. Prior to his doctoral studies, he served as a Research Assistant at the University of Magdeburg in Germany, where he contributed to innovative research in his field. Andreas pursued his education in Industrial Engineering with a concentration on production engineering, acquiring valuable knowledge and skills that have proven to be invaluable in the filed of additive manufacturing.
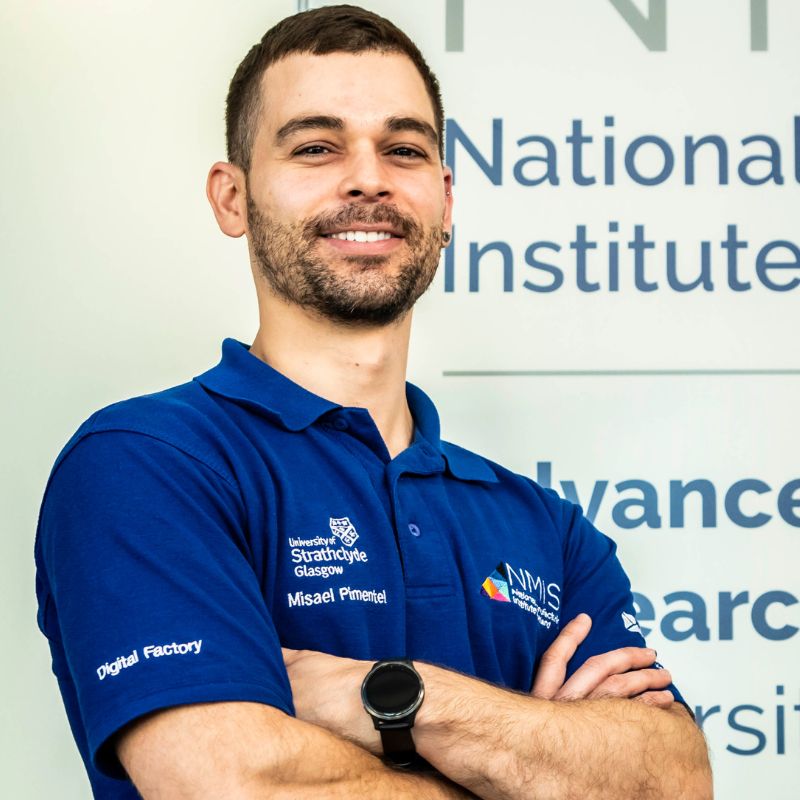
Misael Pimentel
Direct Energy Deposition (DED) Arc Theme Lead, Digital Factory
Misael is currently the Direct Energy Deposition (DED) Arc Welding Theme Lead at the National Manufacturing Institute Scotland, where he has been working for over four years. Prior to this role, he served as a KE Associate Manufacturing Engineer. With a PhD in Arc Welding technologies, his expertise lies in process optimisation for advanced joining techniques, with a background in research, business development, and project management. Misael holds experience in various industries, including internships at Unilever and Lloyd's Register, and research roles with FAPESP and the National Council for Scientific and Technological Development (CNPq). He also holds an exchange Bachelor's degree from the University of Strathclyde, where his research focused on solving complex industrial problems using computational methods.
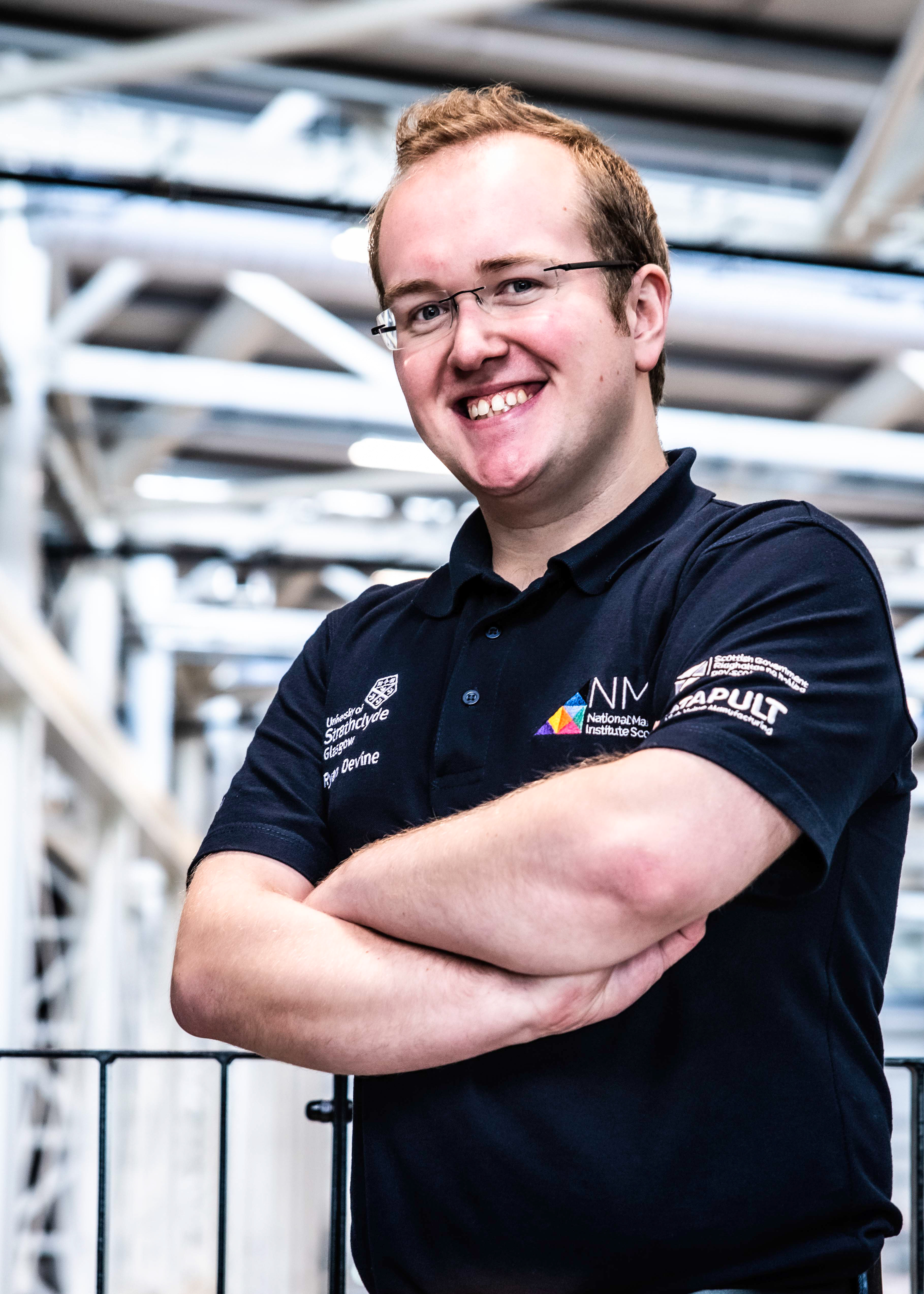
Ryan Devine
Research & Development Engineer, Digital Factory
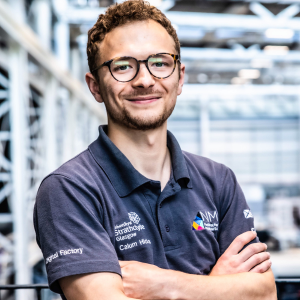
Calum Hicks
Research & Development Engineer, Digital Factory

Ashfaq Mohammad
Senior Research And Development Engineer, Digital Factory
With approximately seven years of experience in Additive Manufacturing-based research, Ashfaq possesses a hands-on expertise in Arcam’s Electron Beam Melting (EBM), FDM, and SLA machines. Having undergone advanced-level training to develop new material themes on the Arcam A2 machine, he has demonstrated a commitment to expanding his skill set. As a Principal Investigator, he has successfully completed a funded project valued at 0.4 million USD. Leading a three-member team, he focused on developing new themes for constructing pore-free parts from Titanium Aluminide using the EBM process. Surpassing initial project goals, the team achieved the production of highly porous components with struts as thin as half a millimeter. Additionally, Ashfaq has collaborated with dental surgeons to design customized implants for patients in Saudi Arabian hospitals, showcasing a multidisciplinary approach to his research.
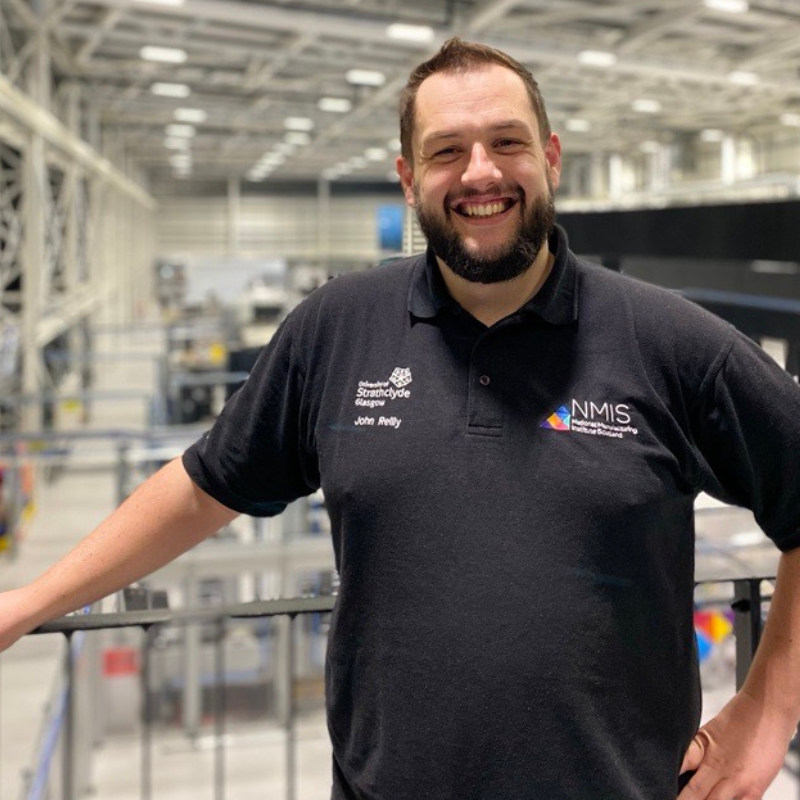
John Reilly
Research & Development Engineer, Digital Factory
John is a versatile professional with experience in various sectors, seamlessly transitioning between roles in electrical and software design. At NMIS, he drives Industry 4.0 initiatives and spearheaded the DEMO project, digitally connecting 73 machines and establishing a private 5G network. Currently leading the ReMake project, John is pioneering a digital framework for product digital passports, promoting traceability and circular economy practices.
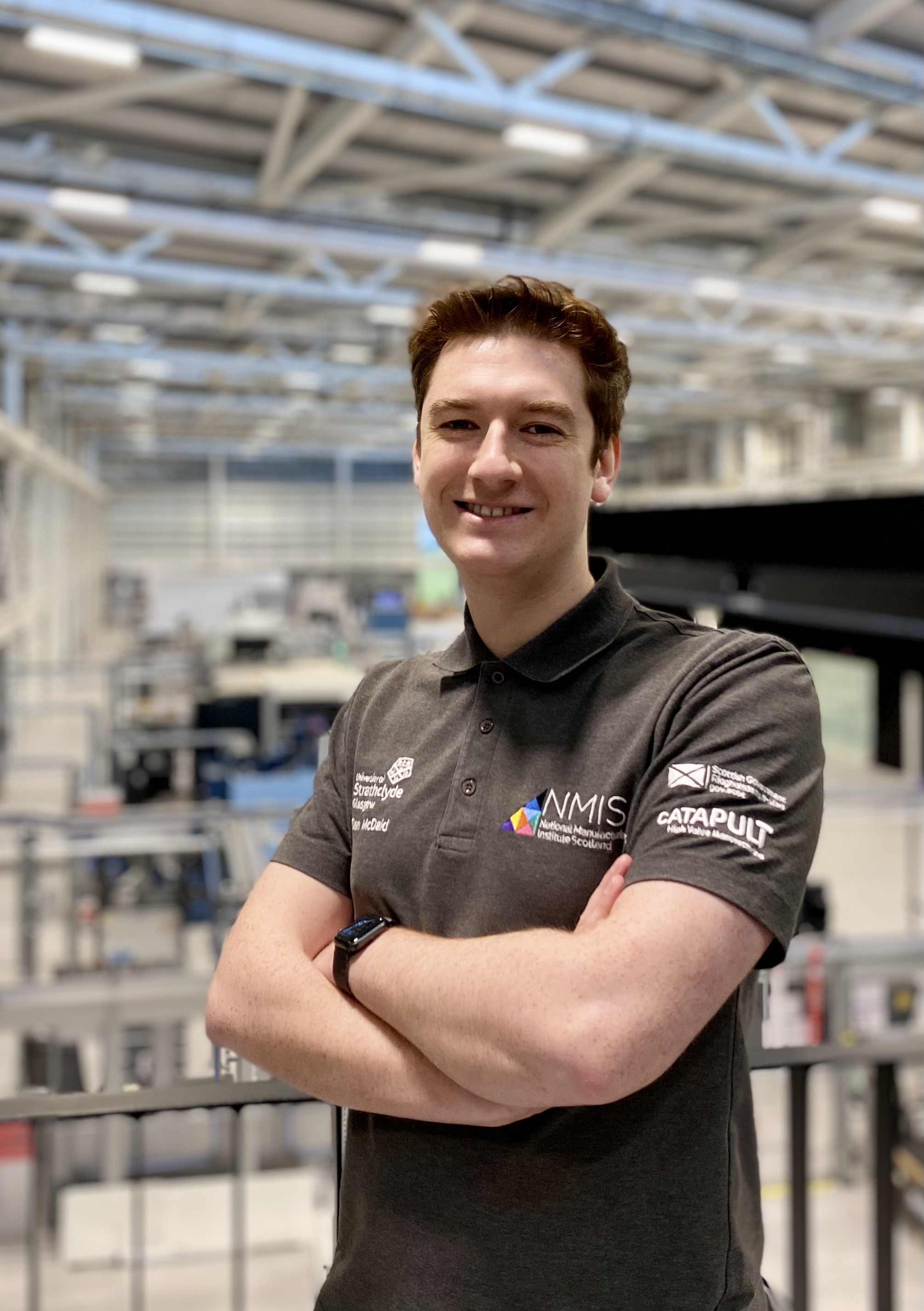
Daniel McDaid
Research & Development engineer, Digital Factory
Dan is a Research and Development engineer in the Design Engineering team. As part of the Verification & Validation / Market Acceptance technical theme, he has been critical in developing the processes, tools, and templates that are now employed across NMIS and within SMEs on a regular basis.
He has also been involved in multiple product development projects across numerous industry sectors, with a focus on capturing product requirements, producing concept designs, and CAD modelling for concept verification.
Prior to NMIS, Dan worked at Belcan where he was primarily involved in the standardisation of Rolls-Royce civil large gas turbine engine components and engine certification programmes to assist with entry into service and passenger safety.
This project is part-funded by the Glasgow City Region Innovation Accelerator programme.
Led by Innovate UK on behalf of UK Research and Innovation, the pilot Innovation Accelerator programme is investing £100m in 26 transformative R&D projects to accelerate the growth of three high-potential innovation clusters – Glasgow City Region, Greater Manchester and West Midlands.
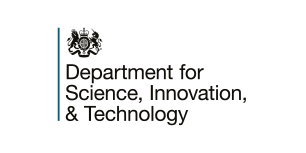
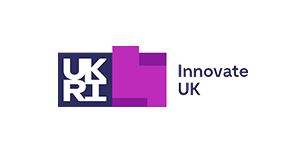
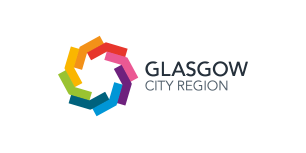
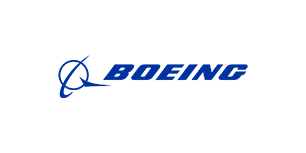
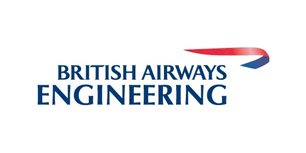
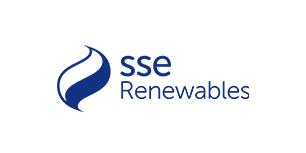
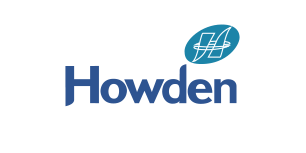
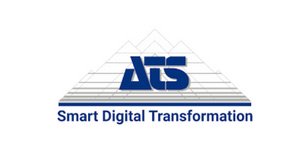
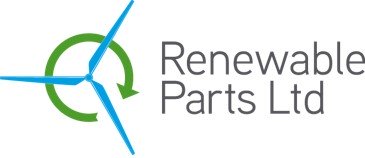
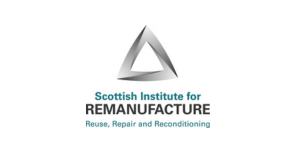