ATI Sprint Hybrid DED
ATI Sprint Hybrid DED - enabling the next evolution in the manufacturing of forged and formed components for the aerospace industry.
As industries gear up to solve the challenges of achieving net zero, critical research is underway to support manufacturers to tackle the emissions resulting from production.
A team of engineers within the National Manufacturing Institute Scotland worked in collaboration with Cranfield University and the Northern Ireland Technology Centre (NITC), to combine the capabilities of traditional metal forging with new techniques such as additive manufacturing and subtractive technologies to deliver near-net-shape components for the aerospace industry. The project concluded in June 2022.
Manufacturing components this way can potentially boost sustainability by reducing the carbon footprint and the amount of raw material required, whilst offering material improvements in the final product.
This game-changing could be applicable across other industries including oil and gas, defence, space, and automotive.
The project
The project partners worked simultaneously to add typical landing gear features using Direct Energy Deposition – ARC, onto different forged substrates using radial forging. These materials were tested and analysed to assess the component properties and potential challenges and limitations for the fabrication of landing gear components.
The development of a subtractive strategy is being created using Parallel Kinematic Machines (PKM) to machine the final demonstrators and compare the PKM with more traditional CNC methods to generate an improved manufacturing step within the Hybrid DED supply chain.
This project was supported by a Steering Group of industry specialists who provided strategic oversight and guidance throughout. They were Airbus, BAE Systems, Dowty Group, Hyde Aero, KUKA, Safran, Spincraft, Spirit AeroSystems, TIMET, and WAAM.
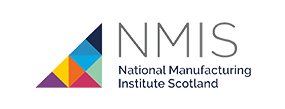
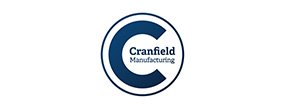
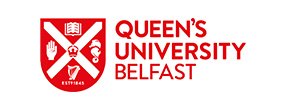
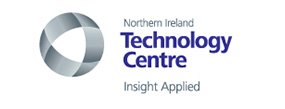
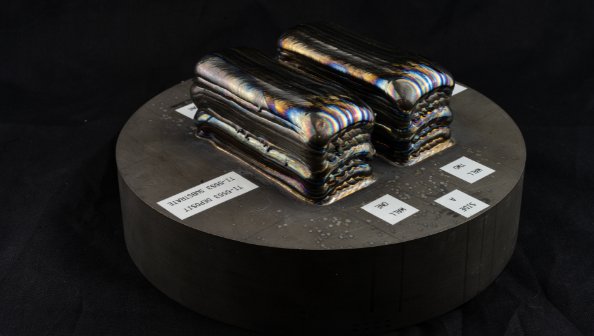
Landing gear-based demonstrator
Work package lead: NMIS and Safran Landing Systems
Using radial forging and Direct Energy Deposition – Arc technologies on a 226mm component, allowed NMIS and Safran to combine two titanium grades (Ti-64 feature onto Ti-5553 substrate) to assess potential challenges and limitations for the fabrication of landing gear components.
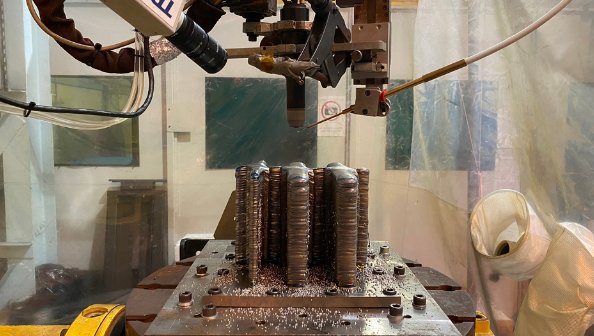
Landing gear-based demonstrator
Work package lead: Cranfield and Airbus
In contrast to NMIS and Safran, Cranfield and Airbus have used one material - 300m steel, fixed onto a 300m steel solid substrate, 700mm in length, to assess the assess potential challenges and limitations for the fabrication of landing gear components.
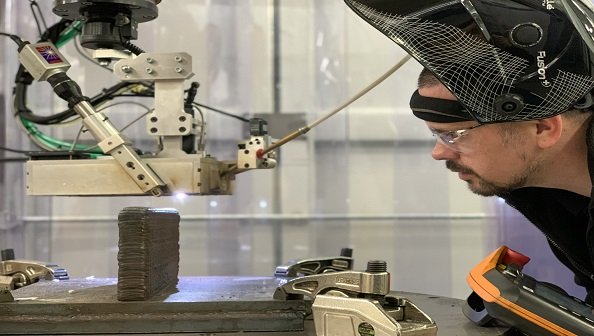
Unconventional machining of final demonstrators
Work package lead: Queens University Belfast / Northern Ireland Technology Centre
Conducting an actual, and virtual force analysis of each component part provided by NMIS and Cranfield has allowed the project team to compare PKM with more traditional CNC methods, by simulating and developing different strategies to help reduce the number of physical tests that need to be carried out.
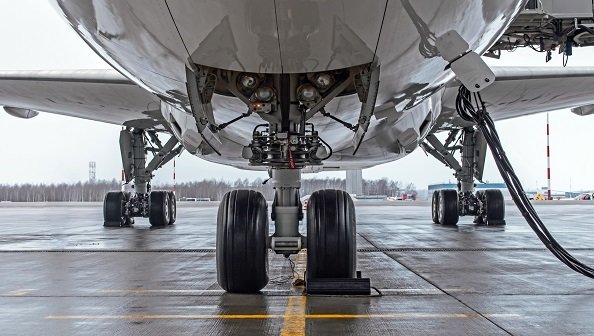
What's next?
When the project draws to a close, the partner's research will be reviewed with the project industrial steering group and the final Hybrid DED manufacturing route will be selected and rolled out to industry where it will help streamline and futureproof production.
Aerospace Technology Institute
This project has been funded by the Aerospace Technology Institute.
The ATI Programme is delivered in partnership with the Department for Business, Energy & Industrial Strategy and Innovate UK. It also works closely with the AGP, the Catapult network, and the UK-ARC academic network.
For further information visit the ATI webpages or follow @UKAeroInstitute.