ACT Blade
Replacing the heavier glass fibre design traditionally used for wind turbine blades with a lighter composite for enhanced efficiency.
Wind energy currently provides up to 15% of Europe’s electricity. To generate more power, wind turbine blades must be longer, which can be difficult as the blades, traditionally made from fibreglass, are often too heavy to lengthen.
The Lightweight Manufacturing Centre (LMC) is working with the University of Sheffield’s Advanced Manufacturing Research Centre (AMRC) and the Offshore Renewable Energy (ORE) Catapult, on an Innovate UK-funded project to help ACT Blade to replace the heavier glass fibre design traditionally used for wind turbine blades with a lighter composite, wrapped in a sail-like textile shell.
The project
Made up of an internal composite structure and high-tech textiles, as opposed to the prevailing fibreglass, ACT’s blades are 24 per cent lighter. A lower weight means blades can be made 10 per cent longer than the standard 55 metre blade around today: producing nine per cent more energy and reducing the cost of energy by 6.7 per cent.
This first of two static tests took place at the Offshore Renewable Energy Catapult’s Blade Test Facility in Blyth. Over three weeks, a full-length blade (13m) withstood the world’s toughest simulation of offshore wind conditions, aimed at testing its structural integrity and durability to the limit.
Upcoming webinars
Did you know we also run our own webinar series?
Our teams host webinars throughout the year. For more information on the upcoming dates and to register, take a look at our events page.
View upcoming webinarsPast webinars
Have you missed out on our previous webinars?
Don’t worry. All our webinars are pre-recorded and added to the NMIS YouTube channel to allow you to catch up on all of the content we have been discussing.
View past webinars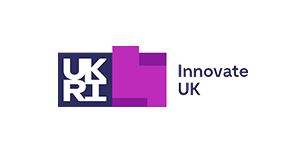