Soltropy
New aluminium design heats up business for Glasgow company
Background
Glasgow based SME Soltropy designs and installs solar water heating arrays. The company currently produces solar water heating technology that is immune to freezing and can be easily integrated into standard heating systems.
Collaborating with the University of Strathclyde's Advanced Forming Research Centre (AFRC), part of the NMIS Group, it was keen to explore an effective aluminium-based alternative for a critical component of its systems, reducing costs and allowing a wider range of customers to be targetted.
Customer challenge
Central to Soltropy's system performance are thermal couplers that transfer the sun's harvested energy from the evacuated tubes to the pipe carrying the fluid to heat.
Soltropy currently uses copper thermal couplers. However, the organisation was keen to switch to aluminium which would provide increased flexibility for manufacturing complex designs, allowing it to expand its product portfolio by producing larger panels.
Given the current cost of materials, aluminium is also likely to be more cost-effective than copper.
How did the AFRC help?
Funded by UKRI's Research and Technology Organisation (RTO) Growth Fund, the AFRC's Forming team used its expertise in finite element analysis to carry out a detailed thermal analysis of several coupler designs and materials.
After understanding the current thermal performance of Soltropy's copper coupler, the team successfully predicted the thermal behaviour of three potential design variations based on cast aluminium.
Following another round of analysis, a 3mm design was selected, which provided a more equal distribution of heat across the pipe compared to the alternatives.
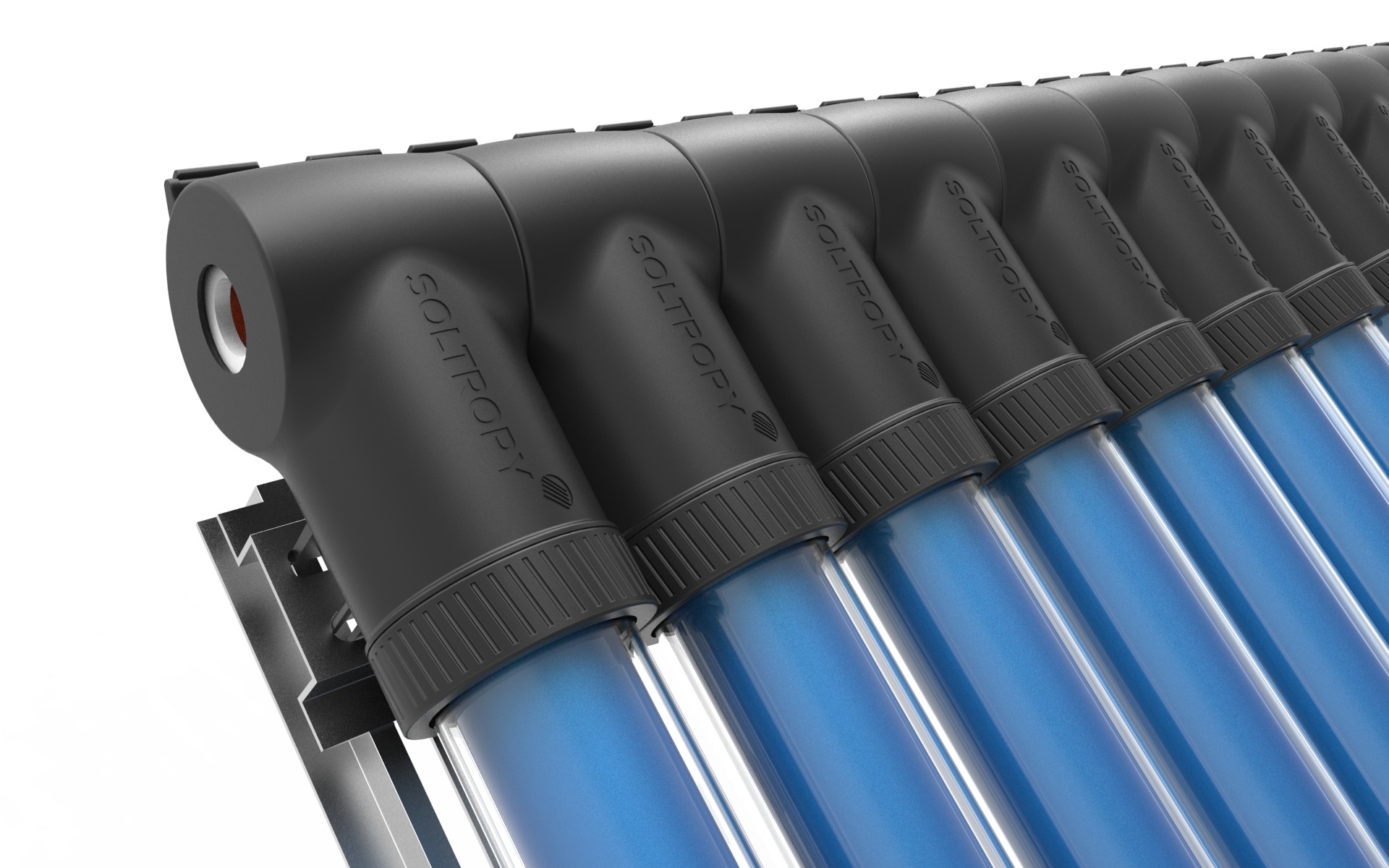
The work carried out by the AFRC enabled us to make an informed decision on the best cost to performance solution allowing us to finalise the new coupler design. Stuart Speake, Founder and CEO, Soltropy
Business Impact
With a new aluminium design, Soltropy can effectively target a broader customer base requiring larger water volumes to be heated. It is also expected that the new solution will yield cost savings over time.
With the AFRC's input, Soltropy has been able to de-risk the material selection process using reliable scientific data to support its decision.
Future collaborations are being explored to investigate the different manufacturing processes that could achieve the best balance of quality and cost in a competitive market.