Sheffield Forgemasters
Simulation speeds Sheffield Forgemasters on its digital journey
Acquired by the Ministry of Defence in August 2021, AFRC Tier One Partner, Sheffield Forgemasters has embarked on a recapitalisation programme with up to £400 million to be invested over ten years to replace defence-critical manufacturing assets.
The firm’s senior leadership team worked closely with some of its key customers within defence and aerospace to explore the potential beneficial role that modelling and virtual simulation could play in the design and development of the new facilities before the acquisition of new equipment.
Customer challenge
Sheffield Forgemasters had prior engagement, good understanding and significant experience of Industry 4.0 technologies including digital modelling and simulation. The team recognised the need to scale up and rapidly deploy modelling and simulation software help shape and ultimately deliver a new forging facility that would set the industry benchmark for productivity, quality and safety.
Having visited high-tech, defence related production facilities in the Midlands and the North West of England to scope options for digital modelling and simulation, Sheffield Forgemasters’ Chief Operating Officer, Gareth Barker, recognised that he would need a manufacturing research partner to work in partnership with his team on a digital journey through uncharted territory, quickly and safely.
Before they set out on this journey, however, they required a production process analysis that would allow the generation of current state requirements and plan for process changes as part of the recapitalisation effort they are undertaking in their machining workshops and Heavy Forge.
How did the AFRC help?
Drawing on the forging expertise of the AFRC and leveraging the digital capabilities within the wider NMIS Group, its leading expert in discrete event simulation (DES) Dr Ruby Hughes, Head of Simulation and Modelling, was embedded within Sheffield Forgemasters’ manufacturing transformation team for a six-month, first phase project.
Her close engagement with the team ensured the work was carried out at an industry pace which was critical to Sheffield Forgemasters. It also enabled the rapid transfer of knowledge to the Sheffield Forgemasters’ transformation leadership team.
Using DES, she was able to model various configurations of the current and possible future states of processes involved in the forging and machining areas of the business. These models were used to verify the operational performance of the processes and facilitated further discussions on implementing changes in the current process within the production environment to meet future state goals.
The first step in this process was to baseline the current manufacturing process by working closely with experts at Sheffield Forgemasters to gain the relevant input information required to run a simulation. This allowed theAFRC to develop a simulation of the process as it currently stands to allow for comparison to alternative machine configurations.
Future state scenarios were then simulated in DES to demonstrate the differences and benefits of proposed solutions and to assist with the decision-making process that surrounds the design and configuration of the overall production process.
The DES approach – which included high level information about cycle times, asset and labour requirements, the method of manufacturing and machine Overall Equipment Effectiveness – was able to identify potential bottlenecks, machine selection and optimisation, and to validate current and potential throughput.
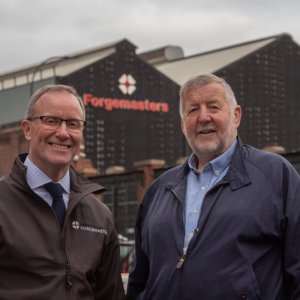
“We have made significant project gains with the embedded support of the AFRC working at our industrial pace. The Sheffield Modelling Team has delivered a set of accurate DES models along our commercial timeline that allows us to be very agile on some of the ‘what-if’ questions from key customers and stakeholders. Not only does this assist the recapitalisation project, but it is also beneficial for the wider future of the business.”
Gareth Barker, Chief Operating Officer, Sheffield Forgemasters
“We will have a digital factory that sits alongside the reality, which is a great place to be thinking about after just six months of intensive effort. The evolving model will enable us to validate our spending: to ensure we get the right kit, with the right people in the right place first time.”
Steve Marshall, Director of Engineering, Sheffield Forgemasters
Business Impact
Over the first six-month phase the AFRC:
- Modelled an accurate visual baseline of the current facility as it is now
- Enabled the testing and validation of future investment options
- Provided the tools to future-proof the new facility’s production capability
- Informed selection of best-fit technology to meet quality and productivity goals
- Equipped Sheffield Forgemasters with simulation and modelling tools to support the recapitalisation strategy.
- Upskilled the recapitalisation ‘transformation team’ in the use of simulation technologies
- Modelled the machine shop to reveal the need for new capabilities to enable Sheffield Forgemasters to expand its portfolio of products and markets
- Began the transition from traditional planning approach to embedding numerical analyses and simulation models and dashboards to support decision making
- Supported a culture of using DES as a "standard" for validating what-If scenarios, future states and Investment options aligned to business partner methodologies
- Established a digital foundation for connected manufacturing journey within Sheffield Forgemasters
- Created a pathway for data standardisation: key for success in digitalisation journey