Scottish Institute for Remanufacturing
Repurposing face masks could prevent 20,000 tonnes of landfill waste each year
Background:
The National Manufacturing Institute Scotland (NMIS), funded by the Scottish Institute for Remanufacturing (SIR), conducted a feasibility study to determine whether the polypropylene component of discarded facemasks could be effectively repurposed into 3D printer filament.
The challenge:
Since March 2020, the UK public has thrown away approximately 53 million disposable face masks each day, with over 20,000 tonnes of waste estimated to have ended up in landfills a year later.
Disposable face masks are typically comprised of three layers; non-woven plastic fabric outer, melt-blown polymer filter such as polypropylene, and non-woven plastic fabric inner. The polypropylene fabric, which amounts to approximately 70-75% of a typical mask, takes over 400 years to biodegrade.
How did NMIS help?
A filament is a substance fed into a heating nozzle in a 3D printer to create, layer by layer, the printed object. The team at NMIS focused on determining whether waste masks could be effectively reused and turned into filament useful for 3D printing.
Firstly, various masks were shredded into pieces before being melted and hot-pressed into sheet plastics. The sheet plastics were then granulated into flakes and fed into the polymer extrusion machine, where they were successfully extruded into filament. Only new masks were used for the study due to hygiene considerations, but the results should apply to waste masks.
Impact:
The team identified a workable solution that could significantly reduce global waste resulting from face masks.
There are opportunities in the future to further explore how the solution could be rolled out on a broader scale, and the costs brought down to make it financially feasible for more companies.
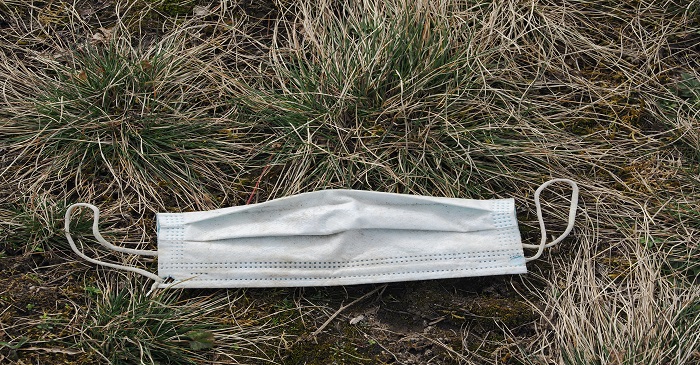
As the world focuses on climate change, this intensifies the spotlight on the utilisation of the world’s finite resources. Remanufacturing is the opportunity to extend the life cycle of these resources and limit landfill and processing, particularly with virgin material. Worldwide health issues like the COVID 19 pandemic have escalated the use of PPE. Therefore, it is exciting to see the potential outcome of this project to extend the life cycle of the polypropylene component.
The Scottish Institute for Remanufacturing is grateful to Zero Wate Scotland for funding this project on the repurposing of PPE.