Rolls-Royce
SPF cycle time reduction
Customer challenge
Rolls-Royce is a global company providing highly-efficient integrated power and propulsion solutions. It is a founding member of the AFRC and uses superplastic forming (SPF) to manufacture hollow wide chord fan blades for aerospace jet engines. With an increasing order book and associated manufacturing volumes, Rolls-Royce needed to investigate the potential to increase its manufacturing capacity by developing techniques to reduce the SPF cycle time for the manufacture of hollow fan blades.
How did NMIS help?
An extensive data mining activity on many years of historic Rolls-Royce manufacturing data for fan blades was managed by AFRC engineers. The team physically integrated themselves within the Rolls-Royce Barnoldswick facility over a period of months – this helped secure first hand understanding of the origins of particular data trends and characteristics.
The SPF cycle was analysed across a number of specific manufacturing cycle stages. Data patterns were established across a range of SPF processing parameters, including temperature, gas pressure and cycletime. These patterns allowed the team to determine the likely factors that would influence component conformity and tool life.
A method for accurate measurement of the SPF temperatures (typically above 900oC) was developed alongside the University of Oxford enabling optimisation of the initial fan blade heating phase of the SPF cycle – the technique was novel and helped secure significant reductions in the time for the fan blades to reach the prescribed SPF temperature.
Full-scale fan blade trials were conducted in the AFRC on a1200 tonne capacity SPF rig, manufactured by ACB (France). Trials were conducted by interrupting the SPF inflation cycle at controlled time intervals, with results then used to establish links and correlations with the initial analysis of the data mining exercise.
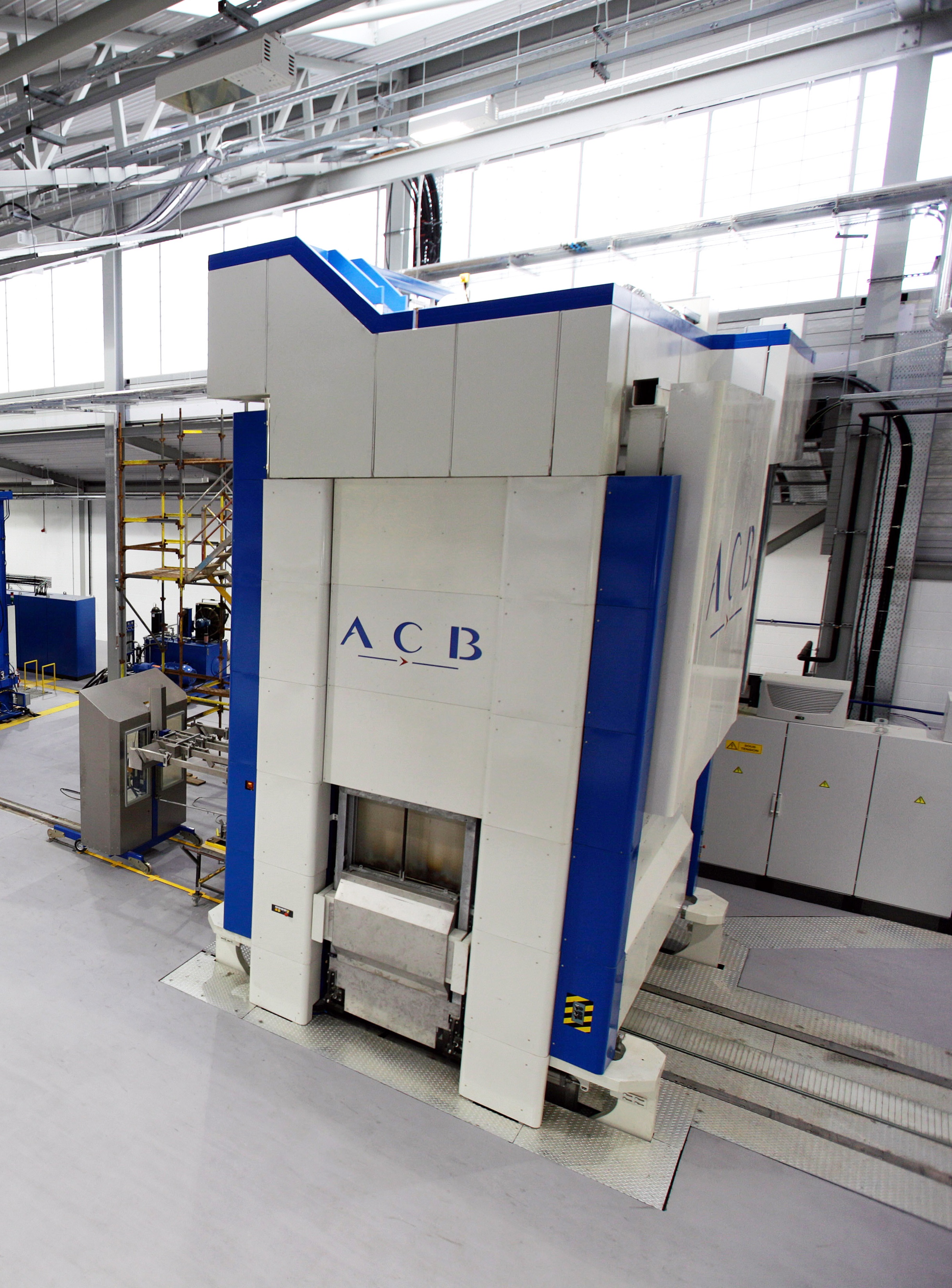
Dr Steven Halliday Rolls-Royce Partnership Manager at the AFRC, stated:
Strong collaboration between the AFRC and Rolls-Royce engineers was needed on this project. The AFRC worked as part of an integrated team, influencing a critical manufacturing process that had historically seen little change….the access to AFRC’s SPF rig was instrumental to achieving the data necessary for validation of the reduced cycle time in a production environment.
Business impact
As a direct result of this project a new SPF inflation curve with a 27% reduction in cycle-time was defined and then validated in production trials within the Rolls-Royce Barnoldswick facility. The reduced SPF process cycle-time has released significant manufacturing capacity to RollsRoyce and has helped avoid forward capital costs associated with new SPF rigs. At project completion the research results were fully implemented into Rolls-Royce’s manufacturing process for fan blades, with minimal disruption to production.