SkiWEDGE
NMIS helps Forfar start-up identify low cost way to make its innovative skiing product
Background
Forfar-based start up SkiWEDGE was set up by Peter Byrne in 2021 to commercialise his innovative training accessory, which aims to make learning to ski easier by ensuring that correct posture is maintained while tackling the slopes.
Customer challenge
SkiWEDGE had successfully developed a concept design, made a selection of prototypes and verified the functional requirements of its product using a physical 3D foam model that sits within a ski boot.
It required support with selecting the best materials and method of manufacture based on important factors such as efficiency, cost, lead time, and supply chain, having already ruled out machining for failing to produce the desired product quality and additive manufacturing for being too time consuming.
How did NMIS help?
In a project funded by an innovation voucher from Interface, the NMIS Design Engineering team collaborated with Peter at SkiWEDGE to understand the product’s essential criteria. After exploring potential material and manufacturing routes, foam was selected as the most cost effective and highest performing material. Compression moulding was identified as the most suitable manufacturing route due to its low cost per unit.
NMIS then supported SkiWEDGE’s engagement with a UK compression moulding manufacturer that suggested modifications to simplify the concept design to reduce manufacturing costs. The NMIS team applied these modifications to a 3D CAD model using SOLIDWORKS.
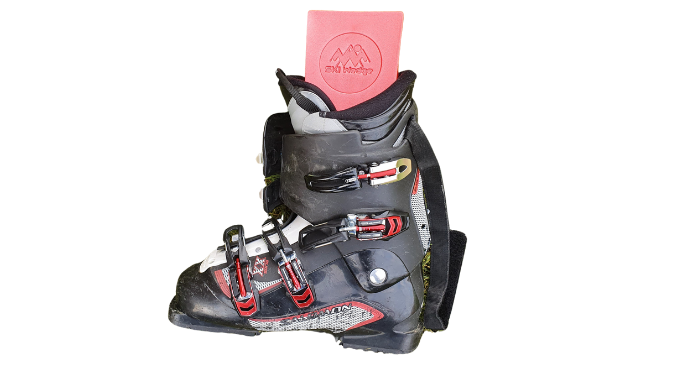
Peter Byrne, SkiWEDGE founder, said:
My experience working with NMIS has been very positive. The project has been well structured, running through the various aspects of product design, from material selection to manufacturing.
"The Design Engineering team has been excellent, with Design Engineer Robert Lynch being very helpful throughout the process and offering guidance and experience, allowing the project to develop and progress.
Business impact
The NMIS Design Engineering team’s systematic approach provided SkiWEDGE with a viable material and manufacturing solution for its skiing teaching and training accessory with the proposed manufacturing route delivering a lower unit cost as production increases.
Collaborating with NMIS at all stages of the development process, the project has exposed Peter to many design methods, materials, and manufacturing processes. With aspirations of developing future product families, this knowledge will support further developments.