DigiTool
Low cost remanufacturing solution can extend the life of manufacturing parts by 120%
As part of a £1.2 million project part-funded by Innovate UK, the National Manufacturing Institute Scotland (NMIS) collaborated with six other project partners to identify a solution to remanufacture dies using additive manufacturing and machining.
Challenge
Dies are used across the hot forging, stamp and press, moulding and oil and gas industries but are subject to high initial costs and long manufacturing lead times.
Historically, there has been little investment in finding a solution to overcome the high costs associated with replacing worn parts not working to their full potential. As a result, organisations are forced to purchase new parts, driving up production costs and raising their carbon footprint.
How did NMIS help?
Toolroom Technology Limited (TTL) led the project, with NMIS specialising in additive manufacturing. The other project partners, Applied Tech Systems (ATS), Hybrid Manufacturing Technologies (HMT), INSPHERE Ltd and Kimber Mills International, delivered research in their areas of expertise, including metrology and scanning, adaptive machining and digital integration.
During the two-year project, the partners developed a new DigiTool framework. It incorporates a three-stage remanufacturing process combining additive manufacturing and machining and can be retrofitted to a legacy machine tool to save entry costs.
As part of the framework, scanning and metrology are initially used to identify worn areas within a part, before additive manufacturing techniques, otherwise known as 3D printing, return the die to “as-new” condition.
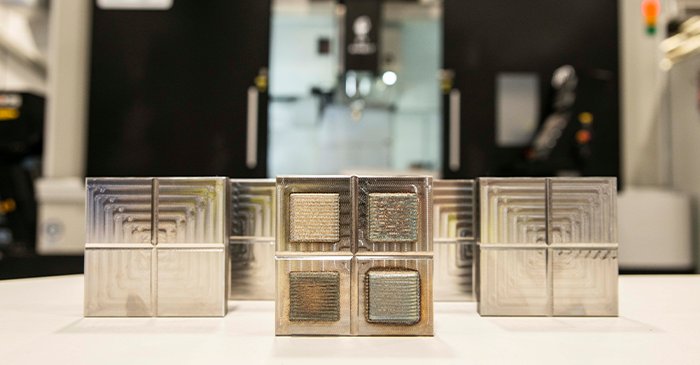
Stephen Fitzpatrick, Machining and Additive Manufacturing team lead at the National Manufacturing Institute Scotland, said:
DigiTool is one the most significant investments of its kind within the tool and die sector for over 40 years. This project has been truly collaborative, and we have combined expertise from a range of backgrounds to answer a challenge that the tool and die sector has been facing for decades.
The DigiTool framework allows manufacturers to upgrade current machinery at a relatively low cost to integrate additive manufacturing and remanufacture on site, extending the lifespan of dies, increasing production output and enhancing their competitive advantage.
Business impact
The DigiTool team has successfully used the framework to help an industrial partner extend the life of a die by 120%, allowing it to make more than double its standard output of complex parts before investing in a new one.
Potentially offering significant production cost savings that can be passed on to end-users, the new DigiTool framework will allow manufacturers to remanufacture on site without transporting materials, thereby reducing environmental impact and saving costs, time and materials.