AFRC helps spring forward mattress preservation technique
Background
Aspire is a Yorkshire-based manufacturer and distributor of mattresses, beds, headboards, and furniture.
Its team of skilled craftspeople construct different types of mattresses at their factory in Morley, using sustainable fabrics from British textile companies and springs sourced from overseas external suppliers.
Challenge
Following production, the mattresses are compressed, rolled, and vacuum-packed to reduce shipping and storage costs, and to minimise their carbon footprint. They can remain compressed for up to nine months before being unpacked by customers at home.
However, this process can affect the mattress’s composition – a common issue in the mattress industry. When springs are used, they are made from thinner wire than flat mattresses. Compression and rolling can damage the coils, especially in the centre, weakening the sides and reducing spinal support, impacting sleep quality, and shortening the mattress’s lifespan.
What did NMIS do?
Funded by Innovate UK through an RTO grant the team at NMIS conducted a series of tests to help Aspire better understand the size variations, internal structure, and chemical composition of the mattress springs.
To improve the reliability of the tests, Aspire provided springs, exhibiting varying behaviour, from two different suppliers.
Engineers from the Advanced Forming Research Centre (AFRC) then performed static and dynamic testing to measure the material’s stiffness under compression and stretching forces. The Rockwell testing method was subsequently used to further analyse the mechanical properties of the springs.
Optical microscopy and energy-dispersive x-ray spectroscopy techniques then provided an insight into the microstructure of the springs and chemical compositions of their materials.
Finally, laser scanning was used to measure the dimensions of the springs, including coil pitch and spring wire length. A bespoke test rig was also designed to expose the measured springs under different loading conditions, including bending, fully compressed and twisting.
The loaded springs were retained in storage for three months before a full scientific review was undertaken. Results were then fed back to Aspire, and the springs were re-tested for another four months at the AFRC.
The next phase of the project will explore the changes in the shape of the springs after time in the controlled load storage experiment, allowing a comparison of the quality of springs supplied. This will help to identify a process for selecting springs that meet the desired performance standard.
The results will then be used to determine the best design for mattresses that can be successfully shipped to customers worldwide.
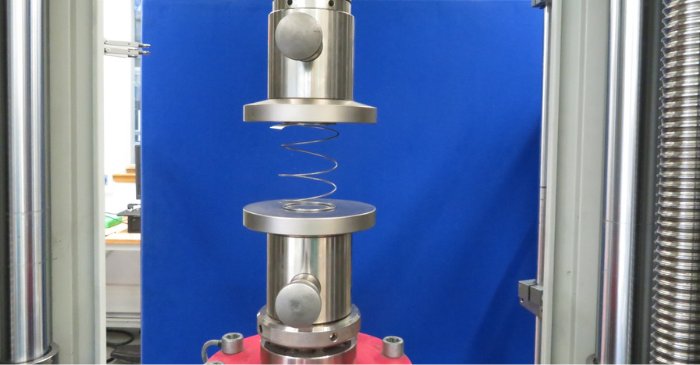
Kit Burgoyne, director of Aspire Manufacturing Ltd, said:
We are committed to delivering exceptional quality across every aspect of our products, but found customers reporting issues with several of our mattresses upon delivery. Working with NMIS has enabled us to better understand the behaviour of our mattresses in storage and will provide valuable insights to help us to actively address potential quality issues with the springs. We look forward to continuing this partnership and applying the project outcomes to enhance our manufacturing process.”
Impact
Once the next phase of the project concludes, Aspire can use the findings to inform the future design of its mattresses and improve customer satisfaction.
Additionally, the project data will allow the team to potentially design and manufacture their own mattress springs, which will remove quality risks from their current supply chain.