ACT Blade
ACT Blade
Background
Currently wind energy provides up to 15% of Europe’s electricity demand and offshore wind is one of the cleanest, cheapest forms of large-scale energy generation in the UK. Industry is always looking for ways to innovate, reduce cost and increase efficiency but to create more power, turbines need longer blades.
A new technology, developed by Edinburgh-based ACT Blade, aims to replace the heavier glass fibre design traditionally used for wind turbine blades with a lighter composite, wrapped in a sail-like textile shell.
Challenge
Most wind turbine blades are made of fibreglass, which is too heavy to be lengthened and expensive to produce. The blades also erode over time and have to be replaced.
ACT Blade planned to adapt technology from the sailing industry and replace the heavier glass fibre design traditionally used for wind turbine blades, with a lighter composite, wrapped in a sail-like textile shell.
This would allow for substantial cost savings and increased production of wind energy.
How did the LMC help?
The Lightweight Manufacturing Centre (LMC) worked with the University of Sheffield’s Advanced Manufacturing Research Centre (AMRC) and the Offshore Renewable Energy (ORE) Catapult, on an Innovate UK funded project to help ACT Blade develop the ultralight and sustainable wind turbine blade and to bring it to market.
Engineers at the LMC applied their lightweighting expertise and composites capabilities to the ACT Blade concept, helping the team to design, test and ultimately manufacture the innovative technology.
Cross Catapult collaboration working produced a prototype for the new blade and static tests were successfully completed at ORE Catapult’s National Renewable Energy Centre in Blyth. The blade will now undergo testing of one million cycles in each direction, with ORE Catapult engineers monitoring its performance.
Business impact
The lighter blade developed as a result of ACT Blade’s collaboration with the AFRC and the wider consortium allows for 10% more length, which, in turn, generates up to 9% more energy from the same wind turbine. Ultimately, the new technology will allow for substantial cost savings and increased production of wind energy.
Manufacturing costs are 30% lower than for conventional blades and as the textile covers the entire surface of the blade, the ACT Blade does not need to be painted. A further benefit is that ACT Blades are component-based and therefore relatively easy to dismantle and separate out for recycling.
The technology could be a disruptor for the offshore wind industry, helping to make offshore wind – already one of the cheapest forms of large-scale energy generation in the UK – even cheaper and easier to harness.
Business impact
The lighter blade developed as a result of ACT Blade’s collaboration with the AFRC and the wider consortium allows for 10% more length, which, in turn, generates up to 9% more energy from the same wind turbine. Ultimately, the new technology will allow for substantial cost savings and increased production of wind energy.
Manufacturing costs are 30% lower than for conventional blades and as the textile covers the entire surface of the blade, the ACT Blade does not need to be painted. A further benefit is that ACT Blades are component-based and therefore relatively easy to dismantle and separate out for recycling.
The technology could be a disruptor for the offshore wind industry, helping to make offshore wind – already one of the cheapest forms of large-scale energy generation in the UK – even cheaper and easier to harness.
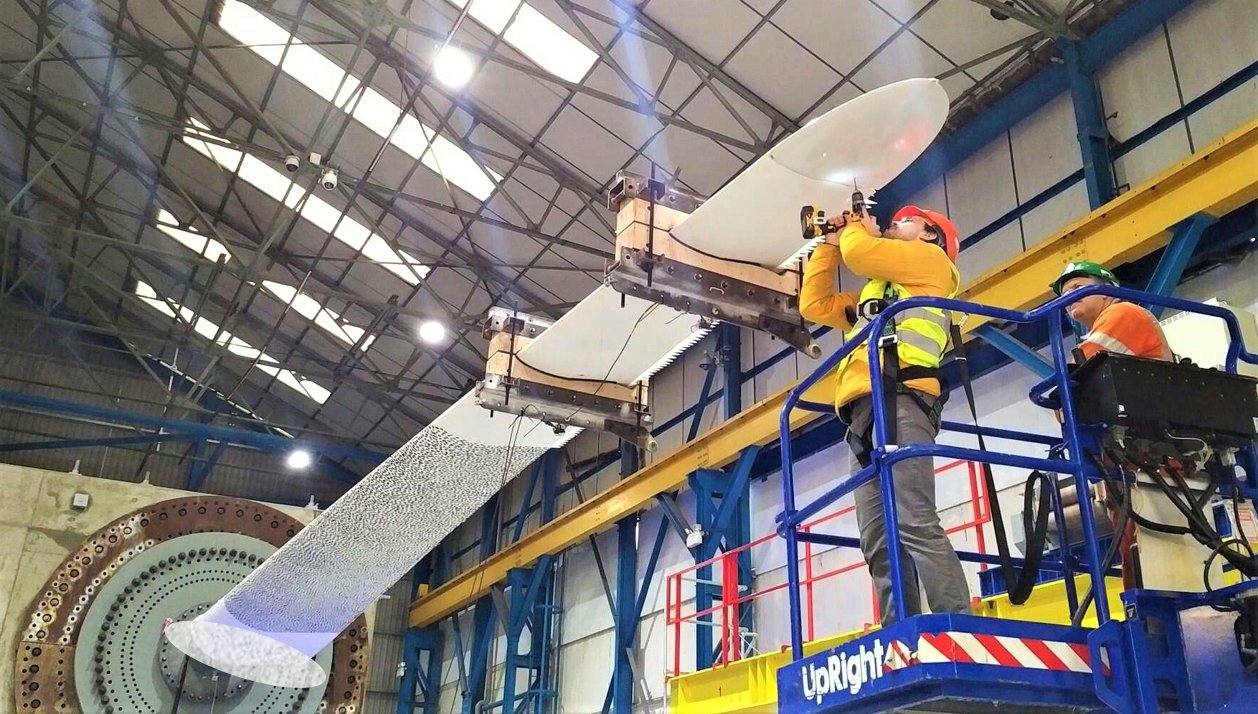
Dr Sabrina Malpede, ACT Blade CEO, said:
Working with the LMC has allowed us to tap into its composite capabilities and take our ACT Blade concept from design through to manufacture. We now have an ultralight blade which has the potential to be completely disruptive to the renewables sector, allowing for substantial cost savings and increased production of wind energy. Now, we need to see how it performs in a real environment.