3D printing helps young entrepreneur’s therapy device blossom
Background
Blossom is a therapy tool designed by Orlando Ely, inspired by his experience supporting family members through stroke rehabilitation. They required a creative and engaging tool to practice motor skills during their recovery, prompting Orlando to develop a solution.
The device features three buildable flowers that challenge fine motor skills and improve cognitive function. Users can arrange the petals and stamen, with each flower offering increasing difficulty. The design encourages both hands to engage in 16 different pinch and grasp exercises.
Additionally, Blossom provides a number of benefits by incorporating natural patterns, reconnecting users with nature, and offering a creative outlet – all of which boost mood and motivation during therapy.
Challenge
After initially creating Blossom with an at-home 3D printer, Orlando faced challenges in scaling the business. He needed additional support to identify the best materials and optimise the design for mass production.
What did NMIS do?
In an R&D project supported with £15,000 of funding from Innovate UK, the NMIS design engineering and additive manufacturing teams worked with Orlando to transform his vision into a commercially viable product. They leveraged advanced 3D modelling techniques to refine Blossom’s design, ensuring it met both aesthetic and functional requirements. The team also evaluated several cutting-edge manufacturing methods, including injection moulding and additive manufacturing processes such as powder bed fusion (PBF) and material extrusion.
PBF emerged as the best option due to its ability to create strong, durable, and highly complex parts with a textured finish, which is crucial for enhancing the tool’s usability. The team also introduced creative design improvements, such as a unique dimple fastening method, further enriching the sensory experience for users.
Impact
With NMIS’s support, Blossom is now ready for commercial production. The refined 3D printed prototypes have allowed Orlando to conduct further user testing, gather feedback, and finalise decisions on manufacturing methods.
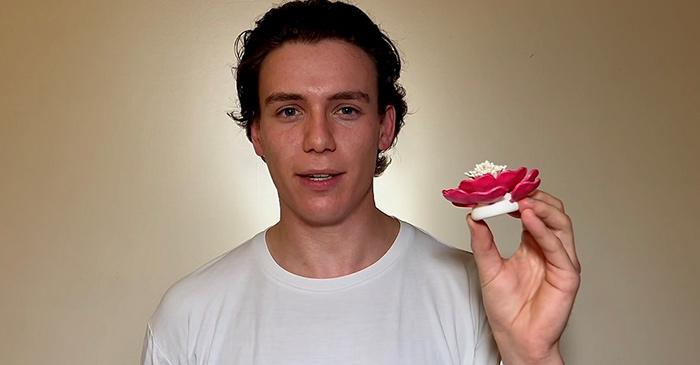
Orlando Ely said:
“With assistance from NMIS to evaluate different manufacturing methods, I'm now well positioned to approach a partner that can manufacture the product at scale. Based on user feedback, my next phase will focus on refining the design, enhancing aesthetic appearance, and expanding the range of therapeutic applications.”