FluidMS
3D printed sensor enclosure opens doors to new markets and cost savings
Background
FluidMS design, develop and manufacture environmental and machine coolant monitoring systems for manufacturing workshops and other industrial environments.
It approached the National Manufacturing Institute Scotland (NMIS) to investigate making a key part in-house instead of buying it off the shelf, which would reduce costs, improve efficiency and provide greater control over its supply chain.
Customer challenge
FluidMS's products incorporate a variety of electronic components fitted into boxes, known as sensor enclosures, which are either mounted directly onto the machines they monitor, or to fixtures around a workshop.
Purchasing the boxes off the shelf, FluidMS had to undertake significant alteration work totalling up to 60 minutes to make the boxes fit for purpose, including adding input/output holes, mounting holes, and Velcro strips to hold internal components in place. This prevents the company from being able to quickly turn around orders.
The boxes were also larger than required, resulting in wasted space and preventing the enclosures from being fitted within tight areas. Certain configurations of the product resulted in just 50% of the enclosure being filled.
How did NMIS help?
In a project funded by the Advancing Manufacturing Challenge Fund’s Additive Manufacturing Business and Technology Support (AM-BATS) project, the NMIS Machining and Additive Manufacturing team determined that additive manufacturing (AM) could be used to create the sensor enclosures.
The AM technologists developed a new enclosure 50% smaller than the existing one through material extrusion AM techology, which does not require any mechanical alterations during assembly.
The team have also upskilled Fluid MS by providing guidance on how to design for AM.
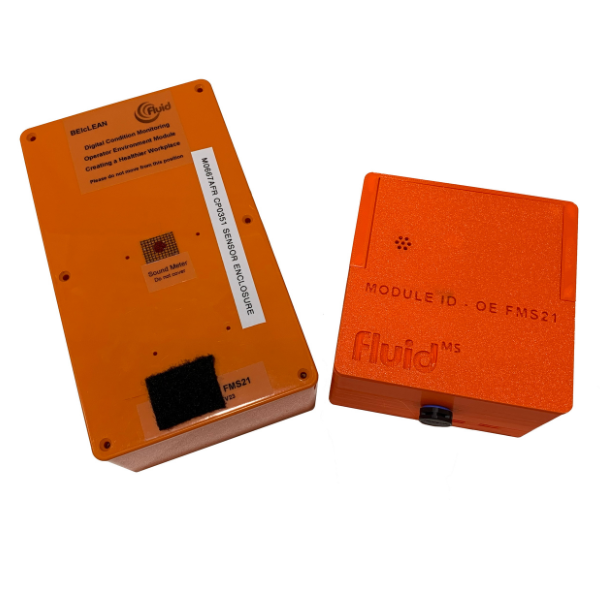
Steve Thompson, Director of FluidMS said:
The advice, guidance, design process and prototypes produced in delivering this project have been exemplary. We knew the change to additive manufacturing was the right decision to help us reduce build costs for our customers' benefit.
“The project has not only proven that but given us the template, knowhow and tools to invest in the technology confidently and pretty much hit the ground running.
Business impact
FluidMS can now manufacture sensor enclosures in-house when they need them, instead of purchasing in bulk from overseas, allowing the company to be responsive to orders and provide quick and efficient service. It can also design bespoke sensor enclosures when launching new products or sensor configurations.
The improvements of the AM design and the removal of the requirement for alterations have reduced the assembly time from 60 to 10 minutes, with production throughput expected to double, allowing for cost savings as demand increases.
Embracing some of the design freedoms offered through AM, FluidMS has also incorporated its company logo and serial numbers into the sensor enclosures, providing the product with a professional finish.