MAPAL
3D demonstrator component showcases tooling performance and attracts new customers
Background
Mapal is a Tier Two Member at the University of Strathclyde's Advanced Forming Research Centre, where it taps into valuable member benefits, including networking opportunities, access to the experts and technical capabilities within the wider National Manufacturing Institute Scotland (NMIS).
Customer Challenge
Mapal provides high-quality machine tooling and offers professional advice on applying it effectively. However, the organisation experienced challenges conveying the quality of its offering within the confines of a trade event.
Aiming to maximise reach and attract new customers at trade events, Mapal required a demonstrator component that would showcase the performance of its tooling, which is dedicated to machining lightweight composite parts.
Using a demo component, Mapal can provide customers with improved confidence in its cutting tools' surface finish quality and lack of delamination.
How did NMIS help?
After an initial discussion regarding Mapal's process and feature requirements, the NMIS Machining and Additive team designed a 3D model of a demonstrator component that incorporated various features to showcase the performance of different tools.
The component was then manufactured from an aerospace-grade carbon fibre composite provided by a key Mapal supply partner to represent real-world manufacturing performance.
Once the design had been finalised, the team from NMIS machined the composite part on the Breton Raptor machine tool at the Lightweight Manufacturing Centre (LMC), an NMIS specialist technology centre.
Mapal supplied the optimal cutting parameters for each tool to achieve the best result.
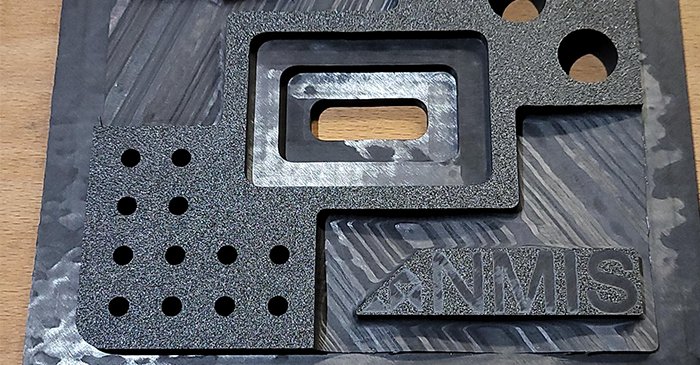
Mark Radcliffe, Business Development Manager, Mapal said:
This demo component was initially for us to use within the UK to showcase the composite range of tooling but, because of the work done at NMIS, we were able to take this part and programme and utilise it as a global Mapal demo part.
“We can now use this component at UK exhibitions and for customers throughout the world.
"Being able to take some work away from our own internal R&D centre helps with the capacity, so collaborations and partnerships like we have with the Advanced Forming Research Centre are critical in helping us to develop our tooling solutions in line with the demanding industry timelines.
Business impact
Mapal now has a physical demonstrator component for showcasing its products and a CAD part that it can manufacture to explain its cutting strategies to customers. This is critical in attracting a broader customer base at global exhibitions.
The component can now be shipped to Mapal's 25 subsidiaries worldwide to use as a demo for attracting new business,